U 2009. godini razvijena je i patentirana tehnologija i oprema za proizvodnju celuloznih poluproizvoda od pšenične slame mehaničkim putem. Posebnost tehnologije je odsutnost otpadnih voda i štetnih emisija.
Proces potpune obrade slame za proizvodnju poluproizvoda od celuloze ne zahtijeva upotrebu bilo kakvih kemikalija ili aditiva, što rezultira odsutnošću kemijske kontaminacije
Kao rezultat korištenja razvijene tehnologije i opreme, moguće je učinkovito dobiti celulozni poluproizvod za daljnju proizvodnju ambalažnog papira ( valovitog kartona, kraft papir, nebijeljeni karton, itd.), i posuđe za jednokratnu upotrebu, pluća Građevinski materijal, pakiranje industrijskih proizvoda, a iz otpada dobiti prah za proizvodnju bioloških gnojiva, što omogućuje gotovo 100% iskorištenje sirovina.
Osim toga, zbog odsutnosti kemijskog onečišćenja, voda se koristi u zatvorenom proizvodnom procesu, čime se ne samo značajno smanjuje potrošnja vode, već se postiže i nulto ispuštanje otpadnih voda.
Ova tehnologija također štedi energiju. Pri proizvodnji celuloznog poluproizvoda kemijskom metodom za dobivanje 1 tone proizvoda potrebno je oko 0,7 tona ekvivalentnog goriva i 100 kW/h električne energije, što je ekvivalentno potrošnji 0,75 tona ekvivalentnog ugljena. Prilikom korištenja mehanička metoda potrebno je samo oko 800 kW/h električne energije, što je ekvivalentno potrošnji od 0,25 tona konvencionalnog ugljena.
Osim toga, potrošnja vode po 1 toni proizvoda je samo 3-6 tona naspram 90-190 tona potrebnih za kemijski proizvodnja celuloze.
Fotografije glavnih komponenti linije za proizvodnju poluproizvoda od celuloze od slame:
![]() |
|||
Tehnološki dijagram linije
1 - Dovodni transporter
2 – Rezač slame
3 - Pulper
4 – Stabilizacijski bazen
5 – Kosi pužni transporter
6 – Pročišćivač
7 – Masivni bazen
8 – Koso sito
9 – Mlin s dva diska
10 – Separator
11 – Vijčana preša
12 – Automatski sustav filtracije
13 – Posuda za vodu
Odavno smo navikli da je sve od drveta, ali zapravo nije uvijek bilo tako...
Izrada papira od drva relativno je novi izum. Na primjer, u Sjevernoj Americi papir se sve do 1850. gotovo isključivo izrađivao od recikliranog platna i krpa.
Na primjer, novčanice, dolari, izrađivane su od lana (25 posto) i pamuka (75 posto). Rezultirajući papir je grub i baršunast, elastičan i izdržljiv, neutralna boja, prošaran najmanjim sintetičkih vlakana(crvene i plave dlake). Kruže glasine da se za proizvodnju ovog papira koriste i vlakna konoplje - zato je dolar tako elastičan i otporan na gužvanje. Međutim, službeno.
Snažan zaokret u zakonima tijekom ere industrijalizacije uveo je porezne poticaje i povoljne vozarine u kasnim 1800-ima, razvoj koji je čvrsto učvrstio papir kao primarni materijal. Ovi poticaji ostaju relevantni do danas i veliki su dio naše ovisnosti o ugroženim šumama za potrebe papira.
Tijekom Drugog svjetskog rata do 1960. u Sjedinjenim Državama bilo je 25 tvornica koje su još uvijek proizvodile papir od pšenične slame.
Više od 20% papira proizvedenog u Indiji i Kini proizvodi se od pšenične i rižine slame i trske. (stabljike ostataka šećerne trske se drobe kako bi se iz njih izvukao sok, a zatim se koriste vlakna).
Globalno, 8% svih proizvoda od papira proizvodi se od poljoprivrednog otpada.
Svake godine milijuni tona poljoprivrednih ostataka od pšenice i lanene slame ostaju neiskorišteni dok se proizvodnja papira i dalje ubrzava. Prema različitim procjenama, to dovodi do sječe oko 830 milijuna stabala svake godine samo u Sjedinjenim Državama.
6 zanimljivih i nevjerojatnih činjenica o proizvodnji papira
1. Za proizvodnju 1 tone papira utroši se 98 tona ostalih resursa;2. Pri proizvodnji 1 tone papira troši se onoliko električne energije koliko je potrebno za proizvodnju 1 tone čelika;
3. Krčenje šuma dovodi do više klimatskih promjena nego svi štetni automobili na svijetu;
4,45% svih ispisanih primjeraka se baci do kraja dana;
5.Svaki stanovnik Sjeverna Amerika Europa godišnje potroši 200 kg papira, dok Afrikanci potroše samo 6,5 kilograma.
6. Nitko na svijetu ne reciklira toaletni papir.
Od čega se pravi papir?
Sada unutra različite zemlje pojavljuju se poduzeća koja aktivno počinju proizvoditi ekološki prihvatljiv papir, što ostavlja minimalan ugljični otisak. Američka baza već uključuje više od 500 proizvođača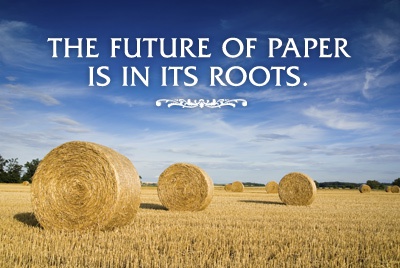
Jedna od tih tvrtki bila je Nature's Paper koja je za proizvodnju uredskog papira počela koristiti slamu pšenice koja ostane nakon žetve žitarica.Obično se slama hrani stokom ili se ostavlja na poljima bez ikakve druge upotrebe osim kao gnojivo.
Nature's Paper skuplja slamu i prerađuje je u papirna masa. No, slama ne daje samo finalni proizvod, već se i zagrijavanje vode za proizvodnju proizvodi organskim gorivom od slame.
Uredski papir izrađen od ovog materijala ima žućkaste boje Stoga se za izbjeljivanje koriste natrijeve soli i klor. Kvaliteta bijeljenog papira apsolutno se ne razlikuje od drvenog papira. Ako bolje razmislite, koliko se starog papira stalno baca zajedno s hranom
Tvrtka daje isključivo primjer pažljiv stav prirodi i maksimalizmu u korištenju poljoprivrednih proizvoda. Ova ideja je za razmišljanje i razvoj sličnih misli u glavama budućih poduzetnika i izumitelja.
Druga tvrtka, New Leaf Paper, proizvodi papir od vlakana banane i palme. Sav papir proizveden u ovom poduzeću nema nikakve veze s drvećem. Naručena je za tiskanje knjiga.
Ecopaper proizvodi papir od svega osim od drveta. Papir s plantaža banana, manga, kave. Pravi se od listova i stabljika ovih biljaka preostalih nakon berbe. Ranije su ih jednostavno bacali, ali sada čine odličan papir. U proizvodnji ovog papira ne koristi se klor. Tu je ovladana i proizvodnja papira od konoplje. Papir izrađen od pogače šećerne trske idealno je bijel, pogodan za upotrebu u uredskoj opremi.
Tvrtka Poopoopaper ovladala je tehnologijom proizvodnje papira od… slonove balege!
Stajnjak se najprije suši, zatim prokuha, dobro opere i koristi za proizvodnju papira. Ne, papir ne miriše ni po čemu i ne razlikuje se izgledom od običnog papira!
Proizvodnja je stavljena u pogon, papir se prodaje u 16 zemalja svijeta.
Na temelju izvora
Više u rubrici
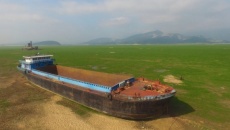
Odavno smo navikli da je sav papir izrađen od drva, ali zapravo nije uvijek bilo tako...
Izrada papira od drva relativno je novi izum. Na primjer, u Sjevernoj Americi papir se sve do 1850. gotovo isključivo izrađivao od recikliranog platna i krpa.
Na primjer, novčanice, dolari, izrađivane su od lana (25 posto) i pamuka (75 posto). Dobiveni papir je hrapav i baršunast, elastičan i izdržljiv, neutralne boje, prošaran sitnim sintetičkim vlaknima (crvene i plave dlačice). Priča se da se za proizvodnju ovog papira koriste i vlakna konoplje, zbog čega je dolar tako elastičan i otporan na gužvanje. Međutim, službeni izvori o konoplji šute.
Snažan zaokret u zakonima tijekom ere industrijalizacije uveo je porezne poticaje i povoljne vozarine u kasnim 1800-ima - razvoj koji je čvrsto učvrstio drvo kao primarni materijal za papir. Ovi poticaji ostaju relevantni do danas i veliki su dio naše ovisnosti o ugroženim šumama za potrebe papira.
Tijekom Drugog svjetskog rata do 1960. u Sjedinjenim Državama bilo je 25 tvornica koje su još uvijek proizvodile papir od pšenične slame.
Više od 20% papira proizvedenog u Indiji i Kini proizvodi se od pšenične i rižine slame i trske. (stabljike ostataka šećerne trske se drobe kako bi se iz njih izvukao sok, a zatim se koriste vlakna).
Globalno, 8% svih proizvoda od papira proizvodi se od poljoprivrednog otpada.
Svake godine milijuni tona poljoprivrednih ostataka od pšenice i lanene slame ostaju neiskorišteni dok se proizvodnja papira i dalje ubrzava. Prema različitim procjenama, to dovodi do sječe oko 830 milijuna stabala svake godine samo u Sjedinjenim Državama.
6 zanimljivih i nevjerojatnih činjenica o proizvodnji papira
1. Za proizvodnju 1 tone papira utroši se 98 tona ostalih resursa;
2. Pri proizvodnji 1 tone papira troši se onoliko električne energije koliko je potrebno za proizvodnju 1 tone čelika;
3. Krčenje šuma dovodi do klimatskih promjena više od štetnih emisija svih automobila na svijetu;
4,45% svih ispisanih primjeraka se baci do kraja dana;
5. Svaki stanovnik Sjeverne Amerike i Europe godišnje potroši 200 kg papira, dok Afrikanci potroše samo 6,5 kilograma.
6. Nitko na svijetu ne reciklira toaletni papir.
Od čega se pravi papir?
Danas se u različitim zemljama pojavljuju tvrtke koje aktivno počinju proizvoditi ekološki prihvatljiv papir koji ostavlja minimalan ugljični otisak. Američka baza već uključuje više od 500 proizvođača
Jedna od tih tvrtki bila je Nature's Paper koja je za proizvodnju uredskog papira počela koristiti slamu pšenice koja ostane nakon žetve žitarica.Obično se slama hrani stokom ili se ostavlja na poljima bez ikakve druge upotrebe osim kao gnojivo.
Nature's Paper skuplja slamu i prerađuje je u papirnatu masu, ali ne samo da slama daje konačni proizvod, već se i zagrijavanje vode za proizvodnju proizvodi fosilnim gorivom napravljenim od slame.
Uredski papir izrađen od ovog materijala ima žućkastu boju, pa se za njegovo izbjeljivanje koriste natrijeve soli i klor. Kvaliteta bijeljenog papira apsolutno se ne razlikuje od drvenog papira. Ako bolje razmislite, koliko se starog papira stalno baca zajedno s hranom
Tvrtka je primjer iznimno pažljivog odnosa prema prirodi i maksimalizma u korištenju poljoprivrednih proizvoda. Ova ideja je za razmišljanje i razvoj sličnih misli u glavama budućih poduzetnika i izumitelja.
Druga tvrtka, New Leaf Paper, proizvodi papir od vlakana banane i palme. Sav papir proizveden u ovom poduzeću nema nikakve veze s drvećem. Naručena je za tiskanje knjiga.
Ecopaper proizvodi papir od svega osim od drveta. Papir s plantaža banana, manga, kave. Pravi se od listova i stabljika ovih biljaka preostalih nakon berbe. Ranije su ih jednostavno bacali, ali sada čine odličan papir. U proizvodnji ovog papira ne koristi se klor. Tu je ovladana i proizvodnja papira od konoplje. Papir izrađen od pogače šećerne trske idealno je bijel, pogodan za upotrebu u uredskoj opremi.
Tvrtka Poopoopaper ovladala je tehnologijom proizvodnje papira od… slonove balege!
Stajnjak se najprije suši, zatim prokuha, dobro opere i koristi za proizvodnju papira. Ne, papir ne miriše ni po čemu i ne razlikuje se izgledom od običnog papira!
Proizvodnja je stavljena u pogon, papir se prodaje u 16 zemalja svijeta.
Vlasnici patenta RU 2447219:
Izum se odnosi na papirnate proizvode od slame žitarica prirodna boja i njihovu proizvodnju. Proizvodi od prirodno obojenog papira imaju bjelinu od 35-60% ISO i proizvode se korištenjem nebijeljene slamnate pulpe s vlačnom čvrstoćom od 230-280 mN, čvrstoćom na savijanje od 40-90 puta i permanganatnim brojem od 16-28. Proizvodi od papira u prirodnoj boji uključuju papirnate maramice u prirodnim bojama, papirnate ručnike u prirodnim bojama, papir za brisanje u prirodnim bojama, fotokopirni papir u prirodnim bojama, papirnate kutije za hranu u prirodnim bojama, papirnate kutije za hranu u prirodnim bojama, prehrambeni proizvodi prirodne boje i papir za tisak u prirodnim bojama. Čvrstoća gore navedenih proizvoda od papira je visoka i kada je sadržaj kontroliran štetne tvari u njima nisu detektirani dioksin i adsorbirani organski halogenidi. 3 n. i 21 plaću f-ly, 20 ave.
Područje tehnologije
Ovaj izum se odnosi na proizvode od prirodno obojenog papira od slame žitarica i metodu za njihovu izradu, točnije, korištenje nebijeljene pulpe slame žitarica kao glavne sirovine za proizvodnju proizvoda od papira prirodne boje i samih proizvoda od papira.
Vrhunac umjetnosti
Papir za kućanstvo jedan je od najrasprostranjenijih artikala; uzimajući u obzir psihološke zahtjeve za stupanj bjeline i neke fizičke pokazatelje, papirna masa se uglavnom proizvodi od bijeljene drvene mase. U nastavku je prikazano nekoliko postojećih tehnoloških rješenja za proizvodnju kućanskog papira.
CN 94105089 odnosi se na svileni papir s visokoučinkovitom ljekovitom supstancom za zdravlje od pšenične slame, tehnologiju proizvodnje papira opisanu u ovoj literaturi, uključujući proizvodnju listova papira.
CN 200410026132 otkriva postupak za proizvodnju papira za kućanstvo od kolagenih vlakana i biljnih vlakana, koji se sastoji od pripreme otopine pulpe od bijeljene pulpe mekog drva i pulpe pšenične slame s masenom koncentracijom od 1% do 4%, zatim se ta otopina pomiješa s celulozom iz kolagena vlakna, dodajte omekšivač u celulozni bazen, zatim se dobiveni celulozni materijal isporučuje u filtar papirnog stroja za ekstruziju, sušenje, predenje kako bi se proizveo proizvod.
Zagađivači iz industrije celuloze i papira uglavnom nastaju u procesima obrade crne lužine i ispuštanja nakon proizvodnje celuloze i izbjeljivanja, posebno nizvodno. Tradicionalne otopine za izbjeljivanje otpada koje sadrže klor sadrže ne samo uobičajene zagađivače vode kao što su KPK i BPK, već i druge specifične zagađivače. Na primjer, kloroform, nastao tijekom procesa izbjeljivanja s kloridom i hipokloritom. Njegov sadržaj u potrošenim otopinama nakon izbjeljivanja jedne tone celuloze s hipokloritom iz bagase šećerne trske iznosi oko 150-250 g, u potrošenim otopinama nakon izbjeljivanja drvne pulpe - oko 700 g. A u potrošenim otopinama za izbjeljivanje s kloridom, osim kloroforma, također postoji više od 40 vrsta organskih klorida, kao što su 2-klorofenol, 3-klorofenol, dioksini i klorofuran, od kojih su mnogi vrlo otrovni. AOX prijeti dovesti do deformiteta, raka i grčevitih promjena.
U zapadnoj Europi, Hong Kongu, Tajvanu, Japanu, Južna Korea Utvrđuju se stroga ograničenja dodavanja štetnih tvari u procesu proizvodnje uredskog papira, zabrana uporabe izbjeljivača i posvjetljivača koji sadrže klor te obvezni zahtjevi za sadržaj štetnih tvari u procesu proizvodnje. U Japanu je postavljeno ograničenje bjeline (ne više od 70%) kako bi se izbjegla pretjerana upotreba slanice. Norma je sljedeća: u otpadnim vodama COD≤20 kg/t papira; AOX≤0,3 kg/t papira. Onečišćenje vode ima visoku cijenu za poduzeća i društvo.
Gore navedeni usporedivi dokumenti koriste pšeničnu slamu ili biljna vlakna kao sirovinu za izradu svilenog papira ili papira za kućanstvo. Zbog zaostalosti postojeće metode Kod izrade pulpe od slame žitarica, uobičajeno je kuhati sirovinu žitarica do niske tvrdoće. Na primjer, za dobivanje kalcijevog permanganata 11-14 potrebno je veliki broj otopina reagensa koji se koriste za kuhanje i dugoročno zagrijavanje i održavanje temperature, što će neizbježno dovesti do mljevenja i oštećenja celuloze i poluceluloze u žitnim sirovinama. Kao rezultat toga, čvrstoća pripremljene slamnate pulpe je relativno niska, a kvaliteta proizvedenog svilenog papira i papira za kućanstvo nije zadovoljavajuća. Osim toga, u procesu proizvodnje svilenog papira i papira za kućanstvo, postojeća tehnologija zahtijeva korak izbjeljivanja, što će dovesti do kontaminacije okoliš i sami proizvodi. Nastali dioksini i adsorbirani organski halogenidi su tvari izazivanje raka; No, u procesu izrade papira od drvne mase, današnja tehnologija zahtijeva dodavanje posvjetljivača i drugih štetnih tvari, čiji ostatak u određenoj mjeri ugrožava zdravlje korisnika.
Stoga, s obzirom na nedostatke sadašnje tehnologije industrije papirne mase i proizvodnje papirne mase veće kvalitete iz slame žitarica, predstavljamo ovaj izum.
Glavni cilj ovog izuma je proizvodnja proizvoda od papira od slame žitarica prirodne boje, što uključuje papirnate maramice prirodne boje, papirnate ručnike prirodne boje, papir za brisanje prirodne boje, fotokopirni papir prirodne boje, kutiju za hranu od papira prirodne boje, omote hrane prirodne boje papir i papir za tisak u prirodnim bojama. Čvrstoća navedenih papirnatih proizvoda je visoka, a praćenjem sadržaja štetnih tvari u njima nisu utvrđeni dioksin i adsorpcijski organski halogenidi.
Za postizanje navedenog cilja koriste se sljedeća tehnološka rješenja.
Papirnati proizvodi prirodne boje proizvode se od sirovine nebijeljene celuloze iz slame žitarica. Bjelina navedenih proizvoda od prirodnog obojenog papira je 25-60% ISO, poželjno je da je bjelina navedenih proizvoda 35-45% ISO.
Duljina loma nebijeljene slamnate pulpe navedene u ovom izumu je 5,0-7,5 km, vlačna čvrstoća je 230-280 mN, vlačna čvrstoća pri ponovljenom savijanju je 40-90 puta, bjelina je 25-45% ISO, stupanj mljevenja pulpe - 32-38°SR; poželjno, duljina loma navedene nebijeljene slamnate pulpe je 6,5-7,5 km, vlačna čvrstoća je 250-280 mN, prekidna čvrstoća je 65-90 puta, stupanj rafinacije pulpe je 32-36°SR, bjelina je 35-45% ISO.
Proizvodi od papira u prirodnoj boji prema ovom izumu uključuju papirnate maramice u prirodnoj boji, papirnati ručnik u prirodnoj boji, papir za brisanje u prirodnoj boji, fotokopirni papir u prirodnoj boji, kutiju za hranu od papira u prirodnoj boji, papir za umatanje hrane u prirodnoj boji i papir za tiskanje u prirodnim bojama.
Proizvodi od papira u prirodnoj boji prema ovom izumu su papirnati papir u prirodnoj boji koji sadrži 70-100% nebijeljene slamnate pulpe i 0-30% nebijeljene drvene pulpe. Visina kapilarnog dizanja tekućine u poprečnom smjeru njezinog produkta je 30-100 mm/100 s, poželjno je da je visina kapilarnog dizanja tekućine u poprečnom smjeru 40-100 mm/100 s, poželjnije je da je proizvod 50-80 mm/100 s.
Vlačna čvrstoća prirodno obojenog svilenog papira ovog izuma je 4-12 Nm/g, poželjno 8-12 Nm/g; mekoća položenog papira - 120-180 mN, po mogućnosti papira - 120-150 mN; gustoća predstavljenog papira je 10,0-18,0 g/m2, poželjno je papir 11,0-13,0 g/m2.
Papirni proizvodi prirodne boje ovog izuma su papirnati ručnici koji sadrže 70-100% nebijeljene slamnate pulpe i 0-30% nebijeljene drvene pulpe. Njegova mokra vlačna čvrstoća u uzdužnom smjeru je 22-55 N/m, poželjno 30-45 N/m.
Visina kapilarnog dizanja tekućine u poprečnom smjeru papirnati ručnik prirodna boja navedena u ovom izumu je 30-100 mm/100 s, poželjno 40-100 mm/100 s, poželjnije 50-80 mm/100 s.
Mekoća i gustoća prirodno obojenog papirnatog ručnika ovog izuma su 120-180 mN i 23.0-45.0 g/m2, poželjno 120-150 mN i 30.0-40.0 g/m2.
Proizvodi od papira u prirodnoj boji prema ovom izumu su kutija za hranu od papira u prirodnoj boji koja je napravljena od 70-100% nebijeljene slamnate pulpe i 0-30% nebijeljene drvene pulpe, čije karakteristike zadovoljavaju zahtjeve za papirnatu kutiju za hranu prema GB 18006.1- 1999 A.
Proizvodi od papira u prirodnoj boji prema ovom izumu su papiri za fotokopiranje u prirodnoj boji koji sadrže 50-80% nebijeljene slamnate pulpe i 20-50% nebijeljene drvene pulpe. Prosječna duljina loma položenog papira u uzdužnom i poprečnom smjeru je 3,2-7,5 km, poželjno 4,5-7,5 km, poželjnije 6,0-7,5 km.
Vlačna čvrstoća fotokopirnog papira u prirodnoj boji ovog izuma je 60-200 puta, poželjno 80-185 puta, kada se više puta savija u poprečnom smjeru.
Gustoća fotokopirnog papira u prirodnoj boji navedenog u ovom izumu je 60.0-75.0 g/m2, poželjno 65.0-72.0 g/m2, poželjnije 69.0-72.0 g/m2 m2; Neprozirnost fotokopirnog papira u prirodnoj boji prema ovom izumu je 82,0-98,0%, poželjno 90-98%.
Papirni proizvodi prirodne boje prema ovom izumu su papiri za omatanje hrane koji sadrže 50-70% nebijeljene slamnate pulpe i 30-50% nebijeljene drvene pulpe. Prelomna duljina mu je 3,2-7,6 km, poželjno 4,5-7,6 km.
Gustoća i čvrstoća na lom nakon ponovljenog savijanja u poprečnom smjeru papir za pakiranje prirodne boje za prehrambene proizvode navedene u ovom izumu su 45-65 g/m2 i 90-200 puta; poželjno 50-60 g/m2 i 120-200 puta.
Poprečna vlačna čvrstoća prirodno obojenog papira za omatanje hrane ovog izuma je 300-600 mN, poželjno 400-600 mN.
Offsetni papir prirodne boje ovog izuma ima bjelinu od 30-60% ISO, njegova pulpa sadrži 65-85% nebijeljene slamnate pulpe i 15-35% nebijeljene drvene pulpe.
Duljina loma offset papira u prirodnoj boji prema ovom izumu iznosi 2,5-5,5 km, a za odabrani offset papir 3,5-5,5 km.
Neprozirnost offset papira u prirodnoj boji prema ovom izumu je 82-98%, a za odabrani offset papir - 85-98%, za više odabrani offset papir - 92-98%.
Vlačna čvrstoća ofsetnog papira u prirodnoj boji prema ovom izumu je 10-35 puta, poželjno 15-35 puta, kada se savije više puta u poprečnom smjeru.
Papirni proizvodi prirodne boje prema ovom izumu su papiri za brisanje koji sadrže 70-100% nebijeljene slamnate pulpe i 0-30% nebijeljene drvene pulpe. Njegova mokra vlačna čvrstoća u uzdužnom smjeru je 22-55 N/m, poželjno 30-45 N/m.
Visina kapilarnog dizanja tekućine u poprečnom smjeru položenog papira za brisanje prirodne boje je 30-100 mm/100 s, poželjno 40-100 mm/100 s, poželjnije 50-80 mm/100 s.
Mekoća i gustoća papira za brisanje prirodne boje su 120-200 mN i 14,0-36,0 g/m2, poželjno 120-180 mN i 18-28 g/m2.
Koraci za proizvodnju nebijeljene slamnate pulpe opisani u ovom izumu uključuju kuhanje i pranje, uklj. dobiti visoko tvrdu slamnatu celulozu s permanganatnim brojem 16-28 i stupnjem mljevenja 10-24°SR nakon kuhanja sirovina iz usjeva žitarica; po mogućnosti s permanganatnim brojem 16-23 i stupnjem mljevenja 10-24°SR.
Priprema gornje nebijeljene slamnate pulpe provodi se prema redoslijedu kuhanja, pranja i delignifikacije kisikom. Delignifikacija kisikom uključuje: pumpanje celuloze s permanganatnom tvrdoćom 16-28 nakon kuhanja uz dodatak lužine i kisika u reaktor stupca za delignifikaciju kisikom; Kao rezultat reakcije delignifikacije nastaje celuloza permanganatne tvrdoće 10-14.
Odabrana delignifikacija kisikom je reakcija u jednom stupnju, ova se reakcija provodi u reaktoru na stupcu za delignifikaciju kisikom; temperatura i tlak ekstrudirane visokotvrde celuloze na ulazu i izlazu iz ovog kolonskog reaktora su redom 95-100°C, 0,9-1,2 MPa i 100-105°C, 0,2-0,6 MPa; u procesu delignifikacije kisikom utrošak lužine (u NaOH) je 2-4% od utroška apsolutno suhe celuloze, utrošak kisika je 20-40 kg/t (apsolutno suhe celuloze); vrijeme reakcije - 60-90 minuta.
Za predmetni izum, slamnata celuloza iz biljaka žitarica dobiva se kuhanjem, pranjem i delignifikacijom kisikom, itd.; Sirovine žitarica uključuju jednu ili više od slame riže, slame pšenice, stabljike pamuka, bagasse šećerne trske, trske ili trske arundo.
Za ovaj izum, proizvodi od papira od slamnate pulpe prirodne boje proizvode se mljevenjem i obradom, izborno dodavanjem određene nebijeljene drvene pulpe i druge pulpe za proizvodnju papira. Zbog činjenice da je gore navedena slamnata pulpa visokokvalitetna nebijeljena pulpa, koja ima visoku čvrstoću i otpornost na lom, a ovi proizvodi od papira nisu bijeljeni, čvrstoća i stopa proizvodnje vlakana se povećavaju za 30-50% odnosno 10%, kao kao i čvrstoća proizvoda od papira povećava se, na primjer, duljina loma itd. Položeni proizvodi od papira u prirodnoj boji mogu uvelike smanjiti stupanj onečišćenja okoliša i izbjeći stvaranje štetnih tvari.
Papirni proizvodi u prirodnoj boji ne sadrže dioksin i organski halid koji se može apsorbirati kada su zagađivači kontrolirani.
Drugi cilj ovog izuma je osigurati metodu za proizvodnju proizvoda od prirodnog obojenog papira.
Za postizanje navedenog cilja koriste se tehnološka rješenja.
Metoda za proizvodnju gore navedenih proizvoda od papira prirodne boje je sljedeća:
(1) dobiti nebijeljenu slamnatu pulpu uzastopno kroz kuhanje, ekstruziju otopine, pranje i cijepanje i delignifikaciju kisikom;
(2) pomiješati gornju nebijeljenu slamu i drvnu pulpu u skladu s tim;
(3) ravnomjerno pomiješati nebijeljenu slamnatu pulpu s nebijeljenom drvenom pulpom ili drugom pulpom za proizvodnju papira u koraku (2) u skladu s traženim masenim udjelom pulpe za proizvode od papira;
(4) izdvojiti pulpu nakon mljevenja i dobiti proizvode od papira prirodne boje.
Korak (3) ove metode nadalje uključuje: tijekom miješanja ili prije miješanja, dodajte potrebne pomoćne reagense za dobivanje papirnatih proizvoda koji nisu posvjetljivači. Ova metoda je na uobičajeni način dobivanje proizvoda od papira korištenjem postojeće opreme.
Dobijte celulozu visoke čvrstoće tvrdoće 16-28 i stupnja mljevenja 10-24°SR nakon kuhanja sirovina žitarica u skladu s korakom (1).
pri kuhanju celuloze metodom amonijevog sulfita, potrošnja amonijevog sulfita iznosi 9-13% potrošnje apsolutno suhih sirovina;
pri kuhanju celuloze metodom antrakinonske sode, potrošnja lužine (u NaOH) iznosi 9-15% potrošnje apsolutno suhih sirovina;
pri kuhanju celuloze sulfatnom metodom, potrošnja lužine (u NaOH) iznosi 8-11% potrošnje apsolutno suhih sirovina;
pri kuhanju celuloze metodom natrijevog sulfita, potrošnja NaOH i natrijevog sulfita je 11-15% odnosno 2-6% težine apsolutno suhih sirovina.
Metoda proizvodnje pulpe navedena u ovom izumu uključuje jednu od metoda amonijevog sulfita, metode antrakinonske sode, sulfatne metode ili metode natrijevog sulfita:
1) pri kuhanju celuloze u kuglastom šaržnom digestoru ili kontinuiranom digestoru:
Opisana metoda amonijevog sulfita uključuje:
(1) dodati otopinu reagensa za kašu biljnom materijalu žitarica, uklj. potrošnja amonijevog sulfita je 9-13% potrošnje apsolutno suhih sirovina, kupka modula 1: 2-4;
(2) zagrijati smjesu vodenom parom na temperaturu od 165-173°C, trajanje porasta temperature, laganog oslobađanja plina i zagrijavanja je 160-210 minuta;
Opisana metoda antrakinonske sode uključuje:
(1) dodati otopinu reagensa za kašu biljnom materijalu žitarica, uklj. potrošnja lužine (u NaOH) je 9-15% potrošnje apsolutno suhih sirovina, modul kupelji je 1: 2-4, a potrošnja antrakinona je 0,5-0,8% potrošnje apsolutno suhih sirovina;
(2) zagrijati smjesu vodenom parom na temperaturu od 160-165°C, trajanje porasta temperature, laganog oslobađanja plina i zagrijavanja je 140-190 minuta;
Opisana sulfatna metoda uključuje:
(1) dodavanje otopine reagensa za kuhanje biljnim sirovinama žitarica s utroškom lužine (NaOH) od 8-11% od utroška apsolutno suhih sirovina, modulom kupelji 1:2-4 i sulfiditetom 5-8%;
(2) zagrijavanje smjese s parom na temperaturu od 165-173°C, povećanje temperature, lagano oslobađanje plina i zadržavanje topline traje samo 150-200 minuta;
(1) dodavanje otopine reagensa za kuhanje biljnim sirovinama žitarica s udjelom lužine (NaOH) od 11-15%, po mogućnosti 9-15% po težini apsolutno suhih sirovina, natrijevog sulfita 2-6% i antrakinona 0,02 -0,08%, kupka modul 1:3-4;
(2) zagrijavanje smjese s parom na temperaturu od 160-165°C, povećanje temperature, lagano oslobađanje plina i zadržavanje topline traje samo 140-190 minuta;
2) kod kuhanja u vertikalnom digestoru:
opisana metoda amonijevog sulfita:
(1) dodati otopinu reagensa za kuhanje biljnim sirovinama žitarica uz utrošak amonijevog sulfita od 9-15% od utroška apsolutno suhih sirovina, modul kupke 1: 6-10;
(2) Biljni materijal žitarica uz pomoć vruće crne luge ulazi u digestor kroz punionicu. Nakon punjenja zatvoriti kotao poklopcem, uliti sredstvo za kuhanje temperature 130-145°C, istovremeno ispumpati zrak iz kotla i povećati tlak na 0,6-0,75 MPa, temperaturu sredstva za kuhanje. do 156-173°C. Porast temperature, zadržavanje topline i zamjena traju samo 220 minuta. Nakon toga upumpajte celulozu u kotao za ispuhivanje;
opisana je metoda antrakinonske sode:
(1) dodajte otopinu reagensa za kuhanje biljnoj sirovini žitarica s utroškom lužine u NaOH od 9-17% od utroška apsolutno suhih sirovina, modul kupelji 1:6-9, utrošak antrakinona od 0,5-0,8 %;
(2) Biljni materijal žitarica uz pomoć vruće crne luge ulazi u digestor kroz punionicu. Nakon punjenja zatvoriti kotao poklopcem, uliti sredstvo za kuhanje na temperaturi od 130-145°C, istovremeno ispumpati zrak iz kotla i povećati tlak na 0,4-0,6 MPa, temperaturu tekućinu za kuhanje na 147-165°C. Porast temperature, zadržavanje topline i zamjena traju samo 170-200 minuta. Nakon toga upumpajte celulozu u kotao za ispuhivanje;
opisana sulfatna metoda:
(1) dodajte otopinu reagensa za kuhanje u biljnu sirovinu žitarica s utroškom lužine u NaOH od 8-13% utroška apsolutno suhih sirovina, modulom kupelji od 1: 6-10 i sulfiditetom od 5 -9%;
(2) Biljni materijal žitarica uz pomoć vruće crne luge ulazi u digestor kroz punionicu. Nakon punjenja zatvoriti kotao poklopcem, uliti sredstvo za kuhanje na temperaturi od 130-145°C, istovremeno ispumpati zrak iz kotla i povećati tlak na 0,5-0,65 MPa, temperaturu tekućinu za kuhanje na 155-168°C. Porast temperature, zadržavanje topline i zamjena traju samo 180-220 minuta. Nakon toga upumpajte celulozu u kotao za ispuhivanje;
Opisana metoda natrijevog sulfita uključuje:
(1) dodavanje otopine reagensa za kuhanje biljnim sirovinama žitarica s potrošnjom lužine od 9-17% po težini apsolutno suhih sirovina, natrijev sulfit 4-8%, antrakinon 0,04-0,08%, modul kupke 1: 6 -10;
(2) Biljni materijal žitarica ubrizgava se u digestor kroz stroj za punjenje pomoću vruće crne tekućine. Nakon punjenja zatvoriti kotao poklopcem, uliti sredstvo za kuhanje na temperaturi od 145°C, istovremeno ispumpati zrak iz kotla i povećati tlak na 0,45-0,6 MPa, temperaturu tekućine za kuhanje na 152°C. -165°C. Porast temperature, zadržavanje topline i zamjena traju samo 180-220 minuta. Nakon toga upumpajte celulozu u kotao za ispuhivanje;
Delignifikacija kisikom opisana u ovom izumu uključuje:
(1) pumpanje dobivene celuloze s permanganatnim brojem tvrdoće 16-28 nakon kuhanja u stupac reaktora za delignifikaciju kisikom i dodavanje lužine i kisika u nju; I
(2) Ova celuloza visoke tvrdoće prolazi reakciju delignifikacije u reaktoru na stupcu za delignifikaciju kisikom i pretvara se u celulozu s permanganatnom tvrdoćom od 10-14.
Odabrana delignifikacija kisikom je jednostupanjska, za njezinu reakciju koristi se kolonski reaktor za delignifikaciju kisikom; temperatura i tlak ekstrudirane visokotvrde celuloze na ulazu u ovaj kolonski reaktor je 90-100°C i 0,9-1,2 MPa, na izlazu - 95-105°C i 0,2-0,4 MPa. U procesu delignifikacije kisikom, utrošak lužine u NaOH je 2-4% od utroška apsolutno suhe celuloze, utrošak kisika je 20-40 kg za 1 tonu apsolutno suhe celuloze; trajanje reakcije - 60-90 minuta.
Upotreba jedne nebijeljene slamnate pulpe u proizvodnji proizvoda od papira prirodne boje, naznačena time što je navedena u zahtjevima 1-3 formule.
Duljina loma nebijeljene pulpe slame navedene u ovom izumu je 5,0-7,5 km, vlačna čvrstoća je 230-280 mN, svjetlina je 25-45% ISO, čvrstoća loma je 40-90 puta, stupanj mljevenja pulpe je 32-38°SR; poželjno, duljina loma je 6,5-7,5 km, vlačna čvrstoća je 250-280 mN, prekidna čvrstoća je 65-90 puta, stupanj rafinacije pulpe je 32-36°SR, stupanj svjetline je 35-45% ISO.
Priprema opisane nebijeljene slamnate pulpe provodi se redoslijedom kuhanja, pranja i delignifikacije kisikom, uključujući učinak kuhanja na transformaciju biljnih sirovina žitarica u celulozu s permanganatnim brojem tvrdoće 16-28 i stupnjem celuloze. mljevenje 10-24°SR, kao i na pretvorbu sirovina biljnih žitarica u celulozu s permanganatnim brojem tvrdoće 16-23 i stupnjem mljevenja celuloze 10-24°SR za pripremu odabrane nebijeljene slame. pulpa.
Poželjno je da se priprema gornje nebijeljene slamnate pulpe provodi prema redoslijedu kuhanja, pranja i delignifikacije kisikom. Delignifikacija kisikom uključuje: pumpanje celuloze s permanganatnom tvrdoćom 16-28 nakon kuhanja uz dodatak lužine i kisika u reaktor stupca za delignifikaciju kisikom; Kao rezultat reakcije delignifikacije nastaje celuloza permanganatne tvrdoće 10-14.
Poželjno je da je delignifikacija s kisikom reakcija u jednom koraku koja se provodi u reaktoru na stupcu za delignifikaciju s kisikom; temperatura i tlak ekstrudirane visokotvrde celuloze na ulazu u ovaj kolonski reaktor su 95-100°C i 0,9-1,2 MPa, na izlazu - 100-105°C i 0,2-0,6 MPa. U procesu delignifikacije kisikom, utrošak lužine u NaOH je 2-4% od utroška apsolutno suhe celuloze, utrošak kisika je 20-40 kg za 1 tonu apsolutno suhe celuloze; trajanje reakcije - 60-90 minuta.
Gore opisano kuhanje jedna je od metoda sulfit-amonijaka, antrakinona-natrija, sulfata i sulfit-natrija.
Pri kuhanju metodom amonijevog sulfita, potrošnja amonijevog sulfita iznosi 9-13% potrošnje apsolutno suhih sirovina.
Pri kuhanju metodom antrakinon-natrij, potrošnja lužine u NaOH iznosi 9-15% potrošnje apsolutno suhih sirovina.
Pri kuhanju sulfatnom metodom, potrošnja lužine u NaOH iznosi 8-11% potrošnje apsolutno suhih sirovina.
Pri kuhanju metodom natrijevog sulfita, potrošnja lužine je 11-15% težine apsolutno suhih sirovina, potrošnja natrijevog sulfita je 2-6% težine apsolutno suhih sirovina.
Navedeno ispiranje:
(1) pumpati pulpu visoke tvrdoće s koncentracijom od 8-15% u prešu, istisnuti crnu tekućinu iz pulpe i dobiti proizvode s koncentracijom od 18-25%; odabrana preša je prijelazna preša, preša s jednim vijkom, dvostrukim vijkom ili dvostrukim valjkom;
(2) za ispiranje pulpe nakon cijeđenja, koje se provodi u vakuumskom ispiraču, tlačnom ispiraču ili vodoravnom trakastom ispiraču, koristi se crna tekućina koncentracije 3-6,2°Be" i pH vrijednosti 8- 8.3 na temperaturi od 70-80°C ili vodu na temperaturi od 70-80°C ili oboje.
S ciljem jasno objašnjenje ovog izuma i njegovih tehničkih inačica, usvojeni pojmovi u ovom izumu imaju sljedeće definicije, koje imaju prednost u slučaju nedosljednosti u bilo kojem drugom dokumentu.
Nebijeljena pulpa slame kako je navedeno u ovom izumu znači pulpa slame koja je pripremljena od jednogodišnje biljke, uključujući, ali ne ograničavajući se na slamu pšenice i riže, stabljike pamuka, šećernu trsku, cane arundo, trsku ili njihove kombinacije, a ne uopće ne prolazi izbjeljivanje, ili pulpa od slame, koja se priprema iz žitarice i podvrgava se delignifikaciji kisikom bez ikakvog drugog izbjeljivanja.
Proizvodi od prirodno obojenog papira u ovom izumu proizvode se korištenjem tradicionalne metode od pulpe slame iz biljaka žitarica kao sirovine bez procesa izbjeljivanja ili s delignifikacijom kisikom bez drugih procesa izbjeljivanja.
U proizvodnji nebijeljene slamnate pulpe navedene u ovom izumu, prije svega, priprema sirovina iz usjeva žitarica se provodi prema postojećoj tehnologiji, odnosno, usvojena je normalna "suha" i "mokra" metoda za žetvu lišća, klasje, zrna, jezgre, zrna pšenice itd. .d., na ovaj način možete smanjiti pritisak u sljedećoj tehnologiji i poboljšati kvalitetu pulpe slame. Kod berbe “suhim” i “mokrim” metodama možete koristiti postojeću opremu, kao što su slamorezač, sito, sakupljač prašine, mokra perilica rublja, kosi valjkasti dehidrator itd. Sirovine iz usjeva žitarica za uklanjanje vode nakon žetve mogu se koristiti kao čisti materijali; sirovine iz usjeva žitarica za uklanjanje vode su apsolutno suhi usjevi s ukupnom duljinom slamki od 15-30 mm. Usvojena tehnologija nabave sirovina poznata je tehničarima u ovoj industriji.
U ovom izumu, drobilica s čekićem može se koristiti za nabavu sirovina korištenjem suhe metode, uključujući sljedeće.
(1) Rezanje i uvijanje žitnih sirovina pomoću drobilice čekića.
Čekićna drobilica u ovoj operaciji uključuje dio za dovod sirovine, dio za drobljenje i uvijanje te dio za odvajanje i izbacivanje. Sirovine okruglog presjeka iz usjeva žitarica spljoštene su pod djelovanjem tlačnih sila, što dovodi do odvajanja listova, osi, zrna, jezgre itd. sa slamom, i pušten iz izlaza drobilice čekića. Duljina proizvedene sirovine iz usjeva žitarica je 20-50 mm.
Postojeća čekić drobilica u ovom izumu služi za pripremu sirovina. Brzina vrtnje mu je 500-800 okretaja u minuti, brzina ulaska sirovina iz usjeva žitarica u čekić drobilicu je 0,5-1,3 m/s. Niska brzina rotacije ili velika brzina punjenja rezultirat će nemogućnošću potpunog uvijanja sirovog materijala, utjecajem prodiranja otopine reagensa za kuhanje i daljnjim utjecajem na kvalitetu pulpe.
Na vanjskoj površini sirovine od usjeva žitarica nalazi se sloj voska, unutar slame nalazi se sloj srži, pri općeprihvaćenom načinu pripreme sloj voska se lako uklanja namakanjem otopine kuhanja. reagensima, ali je sloj srži teško ukloniti zbog zraka unutar slamke, što dovodi do otežanog prodiranja otopine reagensa za kuhanje. Rezanje i uvijanje žitnih sirovina pomoću mlina čekićara olakšava potpunu probavu otopine reagensa za kuhanje, a nakon kuhanja dobiva se visokokvalitetna celuloza.
(2) Uklanjanje prašine sa sirovina nakon rezanja i drobljenja.
Čišćenje sirovina od prašine nakon rezanja i drobljenja usvojeno je kako bi se uklonila većina inkluzija, poput smeća, pijeska, lišća i klasja trave, što može dovesti do smanjenja potrošnje kemijskih reagensa tijekom procesa kuhanja i smanjenja kuhanja vrijeme.
Otprašivač u ovom izumu može se koristiti za pripremu sirovina iz usjeva žitarica, a uključuje valjkasti otprašivač (optimizacija), dvokonusni otprašivač ili ciklonski aparat. Potrošnja zraka ciklona za uklanjanje prašine je 30000-38000 m 3 /h, tlak zraka je 210 mm vodenog stupca. U ovom slučaju moguće je ukloniti većinu prašine u sirovinama iz usjeva žitarica radi lakšeg naknadnog kuhanja.
(3) Prosijavanje sirovina nakon uklanjanja prašine.
Sirovine iz usjeva žitarica nakon uklanjanja prašine često sadrže veliki listovi bilje, komadići i druge nečistoće, tijekom procesa kuhanja, ili neotopljeni predmeti nastaju zbog otežanog prodiranja nekih nečistoća u otopinu reagensa za kuhanje ili uzrokovani povećanjem viskoznosti crne tekućine nakon reakcije drugih nečistoća s otopine reagensa za kuhanje i utjecaj cirkulacije otopine reagensa za kuhanje. Svi navedeni čimbenici dovest će do neravnomjernog kuhanja i poteškoća u radu, utjecaja količine ekstrakcijske crne tekućine i stupnja pročišćavanja pulpe. A prosijavanjem sirovina mogu se izbjeći ti problemi, tako da je postupak prosijavanja vrlo važan za pripremu sirovina iz usjeva žitarica "suhom" metodom.
Cilindrično sito u ovom izumu koristi se za pripremu sirovina iz usjeva žitarica "suhom" metodom, brzina vrtnje mu je 18-29 okretaja u minuti, a kut nagiba je 6-12°. Cilindrično sito ima dvoslojnu strukturu, duljina stranice kvadratne ćelije sita unutarnjeg sloja je 30-40 mm, promjer sitaste ćelije vanjskog sloja je 4-6 mm. U procesu prosijavanja, cilindrično sito može prosijati veliko lišće trave, ostatke itd., osiguravajući stupanj pročišćavanja pulpe.
Učinkovitost uklanjanja nečistoća sirovina iz usjeva žitarica "suhom" metodom prema ovom izumu iznosi više od 90%, a konvencionalnom metodom 70%. Korištenje "suhe" metode navedene u ovom izumu može smanjiti količinu prašine u pulpi, povećati stopu proizvodnje pulpe na 3-6% u usporedbi s konvencionalnom metodom i smanjiti troškove proizvodnje za 2-5%.
Prema ovom izumu, moguće je sirovine prije kuhanja namakati otopinom za namakanje, tako da modul kupelji dosegne 1:2-4. Pri atmosferskom tlaku i temperaturi višoj od 85°C miješa se 10 minuta ili više, bolje se miješa pri temperaturi od 85-95°C 10-40 minuta. Ovo osigurava potpuni kontakt otopine za namakanje sa sirovinom pšenične slame za ravnomjerno i potpuno natapanje sirovine. Kao otopina za namakanje možete koristiti alkalnu otopinu određene koncentracije, koja iznosi (u NaOH) do 4% apsolutno suhih sirovina; Također možete koristiti mješavinu gornje alkalne otopine s crnom otopinom s koncentracijom od 11-14 ° Be "(na 20 ° C). Namakanje sirovina omogućuje cirkulaciju temperature i preostale lužine crne otopine , smanjiti zahtjeve za energijom i resursima i promicati oslobađanje crne tekućine u glavi sa stranim stanicama, hemicelulozom i ligninima koji se oslobađaju tijekom zagrijavanja, pripremiti za naknadno kuhanje. Gornje namakanje sirovina odnosi se na postupak prethodne obrade, svrhu namakanja je pospješiti delignifikaciju tijekom daljnjeg kuhanja.
Pulpiranje sirovine za žitarice je proces uklanjanja lignina iz sirovine, ostavljajući celulozu i hemicelulozu za proizvodnju papira kad god je to moguće. Zbog činjenice da lignini, celuloze, hemiceluloze i drugi sastavi sirovina doživljavaju neke kemijske promjene, degradaciju i oštećenja kada su izloženi visoka temperatura tijekom procesa kuhanja potrebno je proučiti zakon promjene sirovina tijekom procesa kuhanja, kako bi se razvili optimalni uvjeti kuhanja. Primjenom postupka pripreme pulpe u ovom izumu, moguće je smanjiti troškove proizvodnje i uštedjeti potrošnju energije, te povećati prinos pulpe sustavnim proučavanjem potrošnje i koncentracije otopine za kuhanje, vremena kuhanja i držanja, temperature kuhanja, kuhanja , što je više moguće smanjujući oštećenja celuloza i hemiceluloza .
Prema postupku ovog izuma kuhanjem se dobiva visokotvrda celuloza čija je tvrdoća jednaka permanganatnom broju 16-28 (tj. Kappa broju 24-50), stupanj mljevenja je 10-24°SR. ; tvrdoća odabrane celuloze visoke tvrdoće jednaka je permanganatnom broju 18-27 (tj. Kappa broju 29-48); poželjno je da je tvrdoća celuloze najveće tvrdoće permanganatni broj 20-25 (tj. Kappa broj 34-42).
Pulpa visoke tvrdoće pripremljena postupkom kuhanja ovog izuma je sirovina za proizvodnju nebijeljene celuloze. Prilikom korištenja moderne tehnologije Vrijeme kuhanja i držanja je dugo, temperatura kuhanja je visoka, a potrošnja otopine reagensa za kuhanje je velika. A prema metodi navedenoj u ovom izumu, potrošnja otopine reagensa za kuhanje je smanjena, vrijeme kuhanja i držanja je značajno smanjeno. Prema metodi kuhanja specificiranoj u ovom izumu, moguće je smanjiti troškove proizvodnje i uštedjeti potrošnju energije, te povećati prinos celuloze sustavnim proučavanjem potrošnje i koncentracije otopine za kuhanje, vremena kuhanja i držanja, temperature kuhanja, kuhanja procesa i, koliko je to moguće, smanjenje oštećenja celuloza i hemiceluloza. Iskorištenje visokotvrde celuloze prema navedenoj metodi kuhanja je 58-68%.
Prema ovom izumu, nakon kuhanja, dobivena pulpa visoke tvrdoće se razrjeđuje pri određenom tlaku od 0,75 MPa i raspršuje u kotao za ispuhivanje. Razrijeđena otopina može biti gore spomenuta crna tekućina za namakanje. U ovom slučaju, koncentracija visoko tvrde celuloze u kotlu za puhanje je 8-15%, tvrdoća (permanganatni broj 16-28) jednaka je Kappa broju 26-50, kotao za puhanje i pužna preša su povezani prijenosnom pumpom, uz pomoć koje se visokotvrda celuloza transportira iz kotla za puhanje do ulaza u pužnu prešu gdje ulazi visokotvrda celuloza, nakon ekstruzije, ova visokotvrda celuloza izlazi iz pužne preše, koncentracija izlazne celuloze povećava se na 20-28% u odnosu na 8-15%, što je visoko koncentrirana i visoko tvrda celuloza s temperaturom od 70-80 ° C, tijekom ekstruzije celuloze većina crne pulpe se gura u skladišni žlijeb. Odabrana preša koristi se za ekstrakciju crne lužine u sadašnjoj tehnologiji, po mogućnosti preša s jednim vijkom, dva puža ili preša s dva valjka s promjenjivim radijusom i korakom.
Prilikom ekstrudiranja celuloze u preši za puhanje postoji veliki pritisak, temperatura se brzo povećava, što pogoduje odvajanju fibrilacije, fisiji, fibrilaciji, lomu, razaranju primarne stijenke, a celuloza apsorbira dovoljno energije, što rezultira velikim napon, a reaktivnost celuloze visoke tvrdoće jako se povećava. Istodobno se javlja fibroza, površna organska tvar i nečistoće između vlakana su otopljene u isparenoj crnoj tekućini i otpuštene iz žlijeba, a čistoća pulpe je znatno poboljšana. Dio pepela i nečistoća oslobađa se zajedno s crnom tekućinom. U ovom izumu poželjna je pužna preša promjenjivog promjera; zbog promjenjivog promjera, pulpa se ravnomjerno odstranjuje vodom izvana i iznutra u prostoru koji se polako smanjuje. U ovom izumu odabrana je jednopužna preša promjenjivog promjera; nakon ekstrudiranja celuloze visoke tvrdoće, stupanj mljevenja ove celuloze malo se mijenja.
Kada ekstrudirate celulozu, možete koristiti prešu s dvostrukim valjkom, koja vam, poput preše s jednim vijkom, omogućuje smanjenje kidanja vlakana, visok stupanj ekstrakcija crne tekućine pri korištenju ove preše s dvostrukim valjkom omogućuje značajno smanjenje potrošnje vode tijekom pranja u usporedbi s prešom s jednim vijkom; nakon ekstruzije koncentracija visoko tvrde celuloze prelazi 20%, maksimalno je do 25 %.
Prema ovom izumu, kod pranja celuloze visoke tvrdoće potrebno je prvo razrijediti celulozu visoke tvrdoće crnom lužinom koncentracije 11-14 Be" (20°C), dobivenom kuhanjem ili ekstrudiranjem, do koncentracije od 2,5-3,5%, zatim prosijte koristeći postojeću tehnologiju, kao što je vibrirajuće sito, gubitak celuloze u ovom procesu je 0,2-0,5%. Zatim operite vakuumskim ili tlačnim čistačem u postojećoj tehnologiji. Svrha korištenja vakuumski čistač je stvoriti razliku tlaka unutar i izvan stanica celuloze tijekom procesa pranja, što vam omogućuje postizanje povećanog stupnja čišćenja tijekom procesa pranja. Da biste postigli povećani stupanj čišćenja, pranje se može provesti 1 put ili 2 ili 3 puta.
Prema ovom izumu, nakon pranja, koncentracija celuloze kreće se od 9-11%, ova celuloza ulazi u stroj za posipanje kroz puž, stupanj mljevenja prerađene celuloze je unutar 26-28°SR, mokra težina 1,5-1,7 g. , temperatura 65-70°C. Ovaj stroj za odmatanje je postojeća jedinica kao što je visokofrekventni stroj za odmotavanje, stroj za uvijanje, drobilica s diskovima, rafiner s diskovima, odvajač ili separator pulpe. Razmatranjem je moguće olabaviti celulozu i otkriti lignin između celuloza, što je pogodno za daljnju delignifikaciju kisikom.
Visokotvrda celuloza dobivena kuhanjem ili celuloza dobivena otapanjem ili pranjem podvrgava se delignifikaciji kisikom: izbjeljivanje 60-90 minuta pri utrošku lužine (u NaOH) od 2-4% apsolutno suhe celuloze i utrošku kisika od 20-40 kg/t celuloze. U ovom trenutku, tvrdoća celuloze K (permanganatni broj) smanjuje se na 11-13, što je jednako Kappa broju 12,5-17, stupanj mljevenja celuloze je 32-36 ° SR. U ovom izumu, poželjno je da je delignifikacija kisikom jednostupanjska, upotrebom reaktora s jednom kolonom, temperatura celuloze visoke tvrdoće na ulazu u ovaj reaktor je 90-100°C, tlak je 0,9-1,2 MPa, a izlazna temperatura je 95-105°C, a tlak je 0,2-0,4 MPa. Jednostupanjska delignifikacija kisikom koristi se kako bi se osigurala čvrstoća celuloze, u odnosu na višestupanjsku delignfikaciju kisikom, jednostupanjska delignifikacija kisikom ima mala vrijednost za razgradnju celuloze. Među tehnološkim parametrima jednostupanjske delignifikacije kisikom odabranim u ovom izumu karakteristično je niske temperature i relativno dugo kako bi se provela blaga reakcija delignifikacije i što je više moguće izbjegla degradacija celuloze. U ovom izumu, koncentracija odabrane celuloze visoke tvrdoće prije delignifikacije kisikom je u rasponu od 8-18%. Delignifikacija kisikom provodi se pri srednjoj koncentraciji, prednosti: niska ulaganja, zbog tehnologije miješanja i pumpanja srednje koncentracije, obrada pulpe puno je lakša od obrade visoke koncentracije; Pri niskim koncentracijama dolazi do manje korozije opreme i nema opasnosti od izgaranja u kisiku.
Nebijeljena celuloza dobivena u skladu s gornjim operacijama ima prekidnu duljinu od 5,0-7,5 km, vlačnu čvrstoću od 230-280 mN, stupanj svjetline od 25-45% ISO, vlačnu čvrstoću pri ponovljenom savijanju od 40-90 puta, stupanj celuloze mljevenje 32-38 °SR.
Prednost ovog izuma
(1) Nebijeljena celuloza može izbjeći ljudsku štetu od kemikalija koje se koriste u procesu izbjeljivanja, što rezultira proizvodima od papira prirodne boje koji ne sadrže dioksin i karcinogene koji apsorbiraju organske halogenide. Stoga ne šteti ljudima.
(2) Nebijeljena celuloza može smanjiti utjecaj na prekidnu duljinu, vlačnu čvrstoću i prekidnu čvrstoću u procesu bijeljenja, zbog različite metode Rezultirajuća pulpa od slame ima izvanredne karakteristike i može uvelike poboljšati kvalitetu proizvoda od papira prirodne boje.
(3) Prema ovom izumu, pri proizvodnji prirodno obojenih proizvoda od papira od pulpe slame ne dodaje se sredstvo za posvjetljivanje, zbog čega dobiveni proizvodi od papira nisu podložni sekundarnoj kontaminaciji ovom tvari, a proizvodi od papira zadržavaju svoju izvornih svojstava i nisu štetni za ljude.
(4) Zbog poboljšanja metode proizvodnje nebijeljene celuloze u ovom izumu, čvrstoća i karakteristike dobivene nebijeljene celuloze su znatno poboljšane, tako da je moguće koristiti ovu celulozu zajedno s malom količinom drvene celuloze i drugih vrsta celuloze. za izradu proizvoda od papira, a također izravno koristiti pulpu slame za proizvodnju visokokvalitetnih proizvoda od papira.
Specifični koraci proizvodnje
Pšenična slama se obrađuje drobilicom čekićem, zatim se puni u digestor, gdje se dodaje otopina reagensa za kuhanje s amonijevim sulfitom u 9% utroška apsolutno suhe sirovine, kupeljni modul 1:3. Smjesa se zagrijava do 110°C 30 minuta, zatim se podvrgne laganom oslobađanju plina 25 minuta i zagrijava 60 minuta do temperature od 168°C 90 minuta. Tvrdoća celuloze nakon kuhanja je 22, što je jednako Kappa broju 35,5, stupanj mljevenja je 11,6°SR. Pulpa se razrjeđuje crnom tekućinom do koncentracije od 2,5% i prosijava pomoću postojeće tehnologije kao što je vibrirajuće sito. Gubitak celuloze u ovom procesu je 0,5%. Operite celulozu vakuumskom strugačom. Nakon pranja dobiva se visokotvrda celuloza koncentracije 10%, koja se šalje u celuloznu cijev srednje koncentracije i pumpa u kolonu reaktora za delignifikaciju kisikom. Celuloza se miješa u cjevovodu do reaktora na stupcu s kisikom (20 kg/t celuloze) i tekućinom koja sadrži lužine (u NaOH) u omjeru od 4% apsolutno suhe celuloze, zatim se zagrijava s parom. Nakon potpunog miješanja, celuloza s ulaznom temperaturom od 95°C i tlakom od 0,9 MPa sa zaštitnim reagensom magnezijevim sulfatom od 1% do apsolutno suhe celuloze podvrgava se reakciji delignifikacije tijekom 75 minuta pri vršnoj temperaturi od 100° C i tlaka od 0,3 MPa u reaktoru u koloni. U sljedećem koraku, ova se pulpa ubrizgava u bazen i podvrgava ukapljivanju, čime se proizvodi nebijeljena pulpa slame s duljinom loma od 5,0 km, vlačnom čvrstoćom od 40 puta, vlačnom čvrstoćom od 220 mN, svjetlinom od 40% ISO a finoća pulpe 34 °SR. Nebijeljena slamnata pulpa podvrgava se mljevenju, stupanj mljevenja 33°SR, svježa masa 2,1 g. Pripremite nebijeljenu drvnu pulpu sa stupnjem mljevenja 20°SR i sirovom masom 12 g.
Nebijeljena slamnata masa masenog udjela 65% i nebijeljena drvena masa masenog udjela 35% se melju, dobivena smjesa se miješa i obrađuje, nakon čega se dobiva ofset papir prirodne boje. Parametri ovog ofsetnog papira u prirodnoj boji su: gustoća 69,0 g/m2, neprozirnost - 85%, prekidna duljina - 3,9 km, stupanj bjeline - 49% ISO, vlačna čvrstoća pri višestrukom savijanju u poprečnom smjeru 19 puta i otpornost na trganje 258 mN.
Nakon pripreme sirovine od rižine slame suhom metodom, koristeći drobilicu čekićem, pretočiti je u kuglasti šaržni digestor, gdje dodati amonijev sulfit uz 13% utroška apsolutno suhe sirovine, modul kupke je 1:4. Smjesa je zagrijana na 120°C uz vrijeme zadržavanja od 40 minuta, podvrgnuta laganom oslobađanju plina tijekom 25 minuta i zagrijavana 60 minuta do 168°C uz vrijeme zadržavanja od 90 minuta. Tvrdoća i stupanj mljevenja pulpe visoke tvrdoće dobivene nakon kuhanja su 16 (tj. Kappa broj 23) odnosno 23,4°SR, koncentracija pulpe razrijeđene crnom tekućinom je 2,5%; koeficijent gubitka u procesu prosijavanja pomoću postojeće opreme, kao što je vibrirajuće sito, iznosi 0,2%. Operite celulozu vakuumskom strugačom. Nakon toga se vijkom visokotvrda celuloza koncentracije 10% zagrijava na 70°C i transportira u celuloznu cijev srednje koncentracije. Nakon toplinskog poboljšanja ove celuloze u cijevi, ona se pomoću centrifugalne pumpe srednje koncentracije celuloze prenosi u reaktor stupca za delignifikaciju kisika. Prije ulaska u kolonski reaktor, celuloza se u cjevovodu miješa s alkalnom otopinom koja sadrži kisik (20 kg/t celuloze) i 3,5% potrošnje apsolutno suhe celulozne lužine (u NaOH), zatim se zagrijava parom. Nakon potpunog miješanja, celuloza s ulaznom temperaturom od 95°C i tlakom od 0,9 MPa sa zaštitnim reagensom magnezijevim sulfatom od 1% do apsolutno suhe celuloze podvrgava se reakciji delignifikacije tijekom 75 minuta pri vršnoj temperaturi od 100° C i tlaka od 0,4 MPa u reaktoru u koloni. U sljedećem koraku ova se pulpa ubrizgava u bazen i podvrgava ukapljivanju, čime se proizvodi nebijeljena pulpa slame s duljinom loma od 6,8 km, vlačnom čvrstoćom od 50 puta, vlačnom čvrstoćom od 250 mN, svjetlinom od 41% ISO a finoća pulpe 36 °SR.
70% masenog udjela nebijeljene slamnate pulpe i 30% masenog udjela nebijeljene drvene pulpe odvojeno je samljeveno u rafineru s dva diska u koncentraciji od 3,0% odnosno 4,5%. Standard kvalitete pripremljene celuloze: za slamu - stupanj mljevenja 34 ° SR i mokre težine 1,8 g, za drvo - 22 ° SR, odnosno 10 g. Predstavljena drvna masa pripremljena je prema postojećoj tehnologiji, duljina loma je 6,5 km, vlačna čvrstoća 1000 mN, svjetlina 18% ISO, vlačna čvrstoća 1000 puta.
Offsetni papir u prirodnim bojama proizvodi se preradom mljevene homogene celuloze na višecilindričnom stroju za proizvodnju papira s dugim mrežama.
Gustoća postavljenog ofsetnog papira prirodne boje je 70,0 g/m 2, neprozirnost - 84%, duljina loma - 4,9 km, stupanj bjeline - 52% ISO, vlačna čvrstoća pri ponovljenim savijanjima u poprečnom smjeru - 22 puta, otpornost na trganje - 229 mN.
Sirovine iz bagase šećerne trske pripremaju se općeprihvaćenom suhom metodom, nakon vađenja jezgre ulijevaju se u kuglasti digestor, gdje se apsolutno suhim sirovinama, modul kupke, dodaje otopina reagensa za kuhanje s amonijevim sulfitom u 11%. 1: 2,5. Smjesa se zagrijava do temperature od 130°C 20 minuta i podvrgava se laganom oslobađanju plina 20 minuta. Smjesa se zagrijava 50 minuta do temperature od 165°C uz vrijeme zadržavanja od 70 minuta. Tvrdoća celuloze nakon kuhanja je 21, što je jednako Kappa broju 32, stupanj mljevenja je 14,2°SR. Pulpa visoke tvrdoće obrađuje se prešom za crnu lužinu s dva vijka kako bi se postigla koncentracija do 25%, zatim se razrijedi na 2,5% i ispere vakuumskim strojem za čišćenje. Nakon toga se celuloza koncentracije od 10 do 13 % zagrijava pomoću puža na temperaturu od 70 °C i transportira u celuloznu cijev srednje koncentracije. Ta se celuloza fluidizira toplinskim poboljšanjem (uklanjanjem zraka) u cijevi i pumpa centrifugalnom pumpom u reaktor stupca za delignifikaciju kisika. Celuloza se miješa u cjevovodu do kolonskog reaktora s kisikom (30 kg/t celuloze) i tekućinom koja sadrži lužine u NaOH prema težini 3% apsolutno suhe celuloze, zatim se zagrijava parom. Nakon potpunog miješanja celuloze na ulaznoj temperaturi od 98°C i tlaku od 1,05 MPa sa zaštitnim reagensom magnezijevim sulfatom na 0,8% apsolutno suhe celuloze se podvrgava reakciji delignifikacije tijekom 85 minuta na vršnoj temperaturi od 102° C i tlak od 0,4 MPa u reaktorskoj koloni. U sljedećem koraku, ova se pulpa ubrizgava u bazen i podvrgava ukapljivanju, čime se proizvodi nebijeljena pulpa slame s duljinom loma od 6,0 km, vlačnom čvrstoćom na višestrukim savijanjima od 70 puta, vlačnom čvrstoćom od 230 mN, svjetlinom od 40% ISO i finoća pulpe od 35 °SR.
Poželjno je da se 85% težine nebijeljene slamnate pulpe i 15% težine nebijeljene drvene pulpe odvojeno melje u dvostrukom cilindričnom rafineru pri koncentraciji od 3,2% odnosno 4,0%. Standard kvalitete pripremljene celuloze: za slamu - koncentracija 3,2%, stupanj mljevenja 33°SR i svježa masa 2,0 g, za drvo - 4,0%, 18°SR i 11 g, respektivno. Offsetni papir prirodne boje dobiva se obradom mljevene homogene celuloze na višecilindričnom stroju za izradu papira s kratkim i dugim mrežama.
Gustoća ofsetnog papira u prirodnoj boji je 65,0 g/m2, neprozirnost - 85%, duljina loma - 5,5 km, stupanj bjeline - 48% ISO, vlačna čvrstoća pri višestrukom savijanju u poprečnom smjeru - 28 puta, otpornost na trganje - 230 mN.
Sirovine iz trstike arundo pripremaju se drobilicom čekićem i sipaju u kuglasti digestor, gdje se apsolutno suhim sirovinama doda otopina reagensa za kuhanje s 11% amonijevim sulfitom, kupeljni modul 1:3. Smjesa je zagrijana na temperaturu od 140°C uz vrijeme zadržavanja od 40 minuta, podvrgnuta blagom oslobađanju plina tijekom 20 minuta i zagrijavana 60 minuta do temperature od 175°C uz vrijeme zadržavanja od 90 minuta. Tvrdoća pulpe nakon kuhanja je 19, što je jednako Kappa broju 28,5, a stupanj mljevenja je 15,6°SR. Pulpa visoke tvrdoće obrađuje se s prijelaznom jednopužnom prešom dizajniranom za ekstrakciju crne lužine kako bi se postigla koncentracija do 26%, zatim se razrijedi do koncentracije od 2,5 do 3,0% crne lužine, vibracijskim sitom (gubitak celuloze 0,2%) i očišćen od nečistoća sortiranjem (gubitak - 0,1%). Pročišćena celuloza s ulaznom koncentracijom od 2,0% pere se vodoravnom trakom za pranje na temperaturi od 70°C dok izlazna koncentracija ne dosegne 9%. Nakon toga, pulpa se otapa u stroju za odvajanje, u ovom procesu stupanj rafinacije se pretvara sa 24°SR na 27°SR. Zatim se koncentracija celuloze podesi na 10%, zagrijava se na 70°C i transportira u celuloznu cijev srednje koncentracije. Ta se celuloza fluidizira toplinskim poboljšanjem (uklanjanjem zraka) u cijevi i pumpa centrifugalnom pumpom u reaktor stupca za delignifikaciju kisika. Celuloza se miješa u cjevovodu do kolonskog reaktora s kisikom (30 kg/t celuloze) i tekućinom koja sadrži lužine u NaOH pri utrošku 4% apsolutno suhe celuloze, zatim se zagrijava parom. Nakon potpunog miješanja celuloze pri ulaznoj temperaturi od 102°C i tlaku od 1,2 MPa sa zaštitnim reagensom magnezijevim sulfatom uz utrošak od 1% težine apsolutno suhe celuloze, podvrgava se reakciji delignifikacije tijekom 90 minuta pri vršnu temperaturu od 105°C i tlak od 0,5 MPa u reaktorskoj koloni. U sljedećem koraku, ova se pulpa ubrizgava u bazen i podvrgava ukapljivanju, čime se proizvodi nebijeljena pulpa slame s duljinom loma od 7,5 km, vlačnom čvrstoćom od 80 puta, vlačnom čvrstoćom od 280 mN, svjetlinom od 37% ISO a finoća pulpe 33 °SR.
Prikazana nebijeljena slamnata pulpa s masenim udjelom od 50% i nebijeljena drvna pulpa s masenim udjelom od 50% najprije se odvojeno melju u cilindričnom rafineru pri koncentraciji od 3,8%, tlaku od 0,20 MPa i električnoj struji od 62A, zatim u rafineru s dva diska do uvjeta da se postigne koncentracija 3,4%, finoća 35°SR i svježa masa 2,2 g za slamnatu pulpu odnosno 4,5%, 19°SR odnosno 12 g za drvnu pulpu. Predstavljena drvna masa pripremljena je prema postojećoj tehnologiji.
Papir za umotavanje hrane u prirodnoj boji proizvodi se mljevenjem pripremljene pulpe pomoću jednocilindričnog stroja za izradu papira s jednom okruglom mrežom i jednom vunenom tkaninom. Gustoća papira za pakiranje prehrambenih proizvoda u prirodnoj boji je 60,0 g/m2, debljina - 79,0 mikrona, s prednje strane glatka i stražnja strana- 47S i 39S, svjetlina - 20% ISO, neprozirnost - 97,6%, prekidna duljina - 6,8 km, vlačna čvrstoća kod ponovljenih savijanja u poprečnom smjeru - 150 puta, vlačna čvrstoća u poprečnom smjeru - 600 mN, vlažnost - 5,2%.
Trska arundo i trska masenog omjera 1:4 obrađuju se drobilicom čekićem, zatim uz pomoć vruće crne tekućine na temperaturi od 135 °C kroz otvor za punjenje ulaze u digestor, pri čemu se postiže modul kupke do 1:7. Zatvorite poklopac kotla prilikom punjenja, dodajte u kotao otopinu reagensa za kuhanje na temperaturi od 145 ° C uz potrošnju lužine u NaOH od 13% do apsolutno suhih sirovina, antrakinon - 0,5%. Uklonite crnu tekućinu i zrak i povećajte tlak na 0,6 MPa. Zatim uključite recirkulacijsku crpku kotla i cijevni grijač kako biste povećali temperaturu otopine reagensa za kuhanje na 155°C. Povećanje temperature i vrijeme zadržavanja traje samo 160 minuta. Vruća crna tekućina zamjenjuje se razrijeđenom tekućinom i transportira u spremnik vruće crne tekućine. Pulpa nakon kuhanja s tvrdoćom od 20, jednakom Kappa broju od 30 i stupnjem pročišćavanja od 15°SR, podešava se na koncentraciju od 18% i transportira u rafiner s diskom za pročišćavanje, a zatim u cijev za pulpu srednje koncentracije nakon pranja konvencionalnom metodom i naknadnim zagrijavanjem na temperaturu od 70°C pomoću pužnice Ta se celuloza fluidizira toplinskim poboljšanjem (uklanjanjem zraka) u cijevi i pumpa centrifugalnom pumpom u reaktor stupca za delignifikaciju kisika. Celuloza se miješa u cjevovodu do kolonskog reaktora s kisikom (35 kg/t celuloze) i lužnatom otopinom koja sadrži alkalije u NaOH prema težini 2,5% apsolutno suhe celuloze, zatim se zagrijava parom. Nakon potpunog miješanja celuloze na ulaznoj temperaturi od 100°C i tlaku od 1,2 MPa sa zaštitnim reagensom magnezijevim sulfatom na 1% apsolutno suhe celuloze se podvrgava reakciji delignifikacije tijekom 80 minuta na vršnoj temperaturi od 105° C i tlaka od 0,4 MPa u reaktoru u koloni. U sljedećem koraku, ova se pulpa ubrizgava u bazen i podvrgava ukapljivanju, čime se proizvodi nebijeljena pulpa slame s duljinom loma od 7,0 km, vlačnom čvrstoćom od 60 puta, vlačnom čvrstoćom od 240 mN, svjetlinom od 37% ISO a finoća pulpe 37 °SR.
Predstavljena nebijeljena slamnata masa s masenim udjelom od 60 % i nebijeljena drvena celuloza s masenim udjelom od 40 % najprije se odvojeno melju u cilindričnom pročistaču pri koncentraciji od 3,8 %, tlaku od 0,20 MPa i električnoj struji od 65 A. , zatim u rafineru s dva diska pri koncentraciji 3,3%, tlaku 0,15 MPa i električnoj struji 45 A, dok se ne steknu uvjeti da je stupanj usitnjenosti celuloze 48°SR i mokra masa 2,8 g. Predstavljena drvna masa pripremljena je prema postojećoj tehnologiji, njezina duljina loma je 7 km, vlačna čvrstoća je 100 mN, stupanj bjeline - 20% ISO, vlačna čvrstoća nakon ponovljenog savijanja - više od 1000 puta. Stupanj mljevenja nebijeljene slamnate pulpe je 36 ° SR, svježe mase - 2,3 g, drvene pulpe - 20 ° SR, odnosno 12 g.
Papir za pakiranje hrane u prirodnim bojama proizvodi se ekstrakcijom mljevene homogene celuloze.
Gustoća prirodnog papira za pakiranje hrane je 45 g/m2, debljina je 79,0 mikrona, glatkoća prednje i stražnje strane je 45S i 36S, bjelina je 45% ISO, neprozirnost je 97,6%, duljina loma je 5,8 km, vlačna čvrstoća kod ponovljenih savijanja u poprečnom smjeru - 170 puta, vlačna čvrstoća u poprečnom smjeru - 550 mN, vlažnost - 5,3%.
Nakon obrade drobilicom čekićem, trska se ulijeva u kuglasti digestor, gdje se dodaje otopina reagensa za kuhanje s potrošnjom lužine (u NaOH) od 9% i antrakinona od 0,8% do apsolutno suhih sirovina, modul kupelji 1 :4. Smjesa se zagrijava na temperaturu od 110°C uz vrijeme zadržavanja od 40 minuta, podvrgava laganom oslobađanju plina 30 minuta i zagrijava 50 minuta do temperature od 173°C uz vrijeme zadržavanja od 60 minuta. Tvrdoća celuloze nakon kuhanja je 20, što je jednako Kappa broju 30,7, stupanj mljevenja je 12,5°SR. Pulpa visoke tvrdoće obrađuje se prijelaznom jednopužnom prešom za crnu tekućinu kako bi se postigla koncentracija do 20%, zatim se pere konvencionalnom metodom kao što je tlačni skruber. Nakon toga se pulpa otapa u stroju za otapanje, zagrijava na 70°C i transportira u cijev srednje koncentracije pulpe. Ta se celuloza fluidizira toplinskim poboljšanjem (uklanjanjem zraka) u cijevi i pumpa centrifugalnom pumpom u reaktor stupca za delignifikaciju kisika. Celuloza se miješa u cjevovodu do kolonskog reaktora s kisikom (20 kg/t celuloze) i lužnatom otopinom koja sadrži alkalije u NaOH prema težini 4% apsolutno suhe celuloze, zatim se zagrijava parom. Nakon potpunog miješanja celuloze pri ulaznoj temperaturi od 95°C i tlaku od 0,9 MPa sa zaštitnim reagensom magnezijevim sulfatom uz utrošak od 1% težine apsolutno suhe celuloze, podvrgava se reakciji delignifikacije tijekom 70 minuta pri vršnu temperaturu od 100°C i tlak od 0,3 MPa u reaktorskoj koloni. U sljedećem koraku ova se pulpa ubrizgava u bazen i podvrgava ukapljivanju, čime se proizvodi nebijeljena pulpa slame s duljinom loma od 5,8 km, vlačnom čvrstoćom od 55 puta, vlačnom čvrstoćom od 260 mN, svjetlinom od 40% ISO a finoća pulpe 38 °SR.
55% masenog udjela nebijeljene slamnate pulpe i 45% masenog udjela nebijeljene drvene pulpe odvojeno su samljevene u rafineru s dva diska u koncentraciji od 3,5% odnosno 4,5%. Standard kvalitete pripremljene celuloze: za slamu - stupanj mljevenja 35 ° SR i mokre težine 2,0 g, za drvnu pulpu - 20 ° SR i 12 g, respektivno. Predstavljena drvna pulpa je kraft celuloza mekog drveta pripremljena prema postojećoj tehnologiji, njezina duljina loma je 5,0 km, vlačna čvrstoća je 1100 mN, svjetlina je 18% ISO, vlačna čvrstoća je više od 1000 puta, stupanj mljevenja je 39 °SR.
Preradite mljevenu celulozu u papir za pakiranje hrane prirodne boje, gustoće 51,5 g/m2, debljine 75,0 µm, glatkoće prednje i stražnje strane 48S i 36S, svjetline 40% ISO, neprozirnosti 96 ,8%, duljine loma - 3,2 km, čvrstoće loma pri ponovljenim savijanjima u poprečnom smjeru - 140 puta, vlačna čvrstoća u poprečnom smjeru - 380 mN, vlažnost - 5,8%.
Sirovine iz stabljika pamuka pripremaju se drobilicom čekićem i ulijevaju u kuglasti digestor, gdje se apsolutno suhim sirovinama, sulfiditeta 8% i modula kupke 1, dodaje otopina reagensa za kuhanje s utroškom lužine u NaOH od 8 %: 2. Smjesa se zagrijava na temperaturu od 110°C uz vrijeme zadržavanja od 40 minuta, podvrgava laganom oslobađanju plina tijekom 25 minuta i zagrijava 45 minuta do temperature od 166°C uz vrijeme zadržavanja od 75 minuta. Tvrdoća celuloze nakon kuhanja je 22, što je jednako Kappa broju 35, a stupanj mljevenja je 11,6°SR. Ova pulpa visoke tvrdoće otapa se visokofrekventnim dozatorom i obrađuje prešom s dva valjka dizajniranom za ekstrakciju crne tekućine kako bi se postigle koncentracije do 32%. Celuloza se razrijedi razrijeđenom crnom tekućinom do koncentracije od 2,5%, ispere općeprihvaćenom metodom nakon čišćenja od nečistoća. Nakon toga, koncentracija izlazne celuloze doseže do 15%. U sljedećem koraku pulpa se pomoću vijka zagrijava na 70°C i transportira u epruvetu srednje koncentracije pulpe. Ta se celuloza fluidizira toplinskim poboljšanjem (uklanjanjem zraka) u cijevi i pumpa centrifugalnom pumpom u reaktor stupca za delignifikaciju kisika. Celuloza se miješa u cjevovodu do kolonskog reaktora s kisikom (20 kg/t celuloze) i lužnatom otopinom koja sadrži alkalije u NaOH prema težini 3% apsolutno suhe celuloze, zatim se zagrijava parom. Nakon potpunog miješanja celuloze pri ulaznoj temperaturi od 95°C i tlaku od 0,9 MPa sa zaštitnim reagensom magnezijevim sulfatom uz utrošak od 1% težine apsolutno suhe celuloze, podvrgava se reakciji delignifikacije tijekom 90 minuta pri vršnu temperaturu od 100°C i tlak od 0,4 MPa u reaktorskoj koloni. U sljedećem koraku, ova se pulpa ubrizgava u bazen i podvrgava ukapljivanju, čime se proizvodi nebijeljena pulpa stabljike s duljinom loma od 4,3 km, vlačnom čvrstoćom 70 puta, vlačnom čvrstoćom od 275 mN, svjetlinom od 42% ISO a finoća pulpe 34 °SR.
Maseni udio od 80% nebijeljene celuloze stabljike i 20% maseni udio nebijeljene drvne celuloze odvojeno se melju u rafineru s dva diska u koncentraciji od 3,5% odnosno 4,5%. Standard kvalitete pripremljene celuloze: za celulozu stabljike - stupanj mljevenja 55 ° SR i svježa težina 2,0 g, za drvnu celulozu - 48 ° SR i 2,6 g, respektivno. Predstavljena drvna pulpa je kraft celuloza mekog drveta pripremljena prema postojećoj tehnologiji, njezina duljina loma je 5,0 km, vlačna čvrstoća je 1100 mN, svjetlina je 18% ISO, vlačna čvrstoća je više od 1000 puta, stupanj mljevenja je 39 °SR.
Ekstrahirajte mljevenu celulozu kako biste dobili fotokopirni papir prirodne boje, gustoće - 60,0-80,0 g / m2, prosječne duljine loma u uzdužnom i poprečnom smjeru - 4,5 km, uzdužne krutosti na savijanje - 112 mN, poprečnog savijanja - 72 mN, svjetline 44,7% ISO.
Rižine i pšenične slamke masenog omjera 1:3 obrađuju se drobilicom čekićem suhom metodom, zatim ulaze u digestor, gdje se dodaje otopina reagensa za kuhanje uz potrošnju lužine u NaOH od 11% do apsolutnog suha. sirovine, sulfiditet 5% i kupeljni modul 1:4. Smjesa se zagrijava na temperaturu od 110°C uz vrijeme zadržavanja od 20 minuta, podvrgava laganom oslobađanju plina 30 minuta i zagrijava 40 minuta do temperature od 168°C uz vrijeme zadržavanja od 90 minuta. Tvrdoća celuloze nakon kuhanja je 19, što je jednako Kappa broju 29, stupanj mljevenja je 14,3°SR. Pulpa visoke tvrdoće obrađuje se konvencionalnom prijelaznom jednopužnom prešom dizajniranom za ekstrakciju crne tekućine. Izlazna celuloza se razrijedi do koncentracije 3,0% razrijeđenom crnom otopinom i prosije vibrirajućim sitom (gubitak celuloze - 0,2%) i očisti od nečistoća sortiranjem (gubitak - 0,1%). Pročišćena celuloza je isprana s horizontalnom trakom za ispiranje u koncentraciji od 3,0% i temperaturi od 70°C. Nakon toga, izlazna koncentracija doseže do 9%. U sljedećem koraku, pulpa se otapa visokofrekventnim strojem za ljuštenje, fluidizira u cijevi srednje koncentracije pulpe metodom uklanjanja zraka i pumpa centrifugalnom pumpom u reaktor stupca za delignifikaciju kisika. Celuloza se miješa u cjevovodu do kolonskog reaktora s kisikom (20 kg/t celuloze) i lužnatom otopinom koja sadrži alkalije u NaOH prema težini 4% apsolutno suhe celuloze, zatim se zagrijava parom. Nakon potpunog miješanja celuloze pri ulaznoj temperaturi od 95°C i tlaku od 0,9 MPa sa zaštitnim reagensom magnezijevim sulfatom uz utrošak od 1% težine apsolutno suhe celuloze, podvrgava se reakciji delignifikacije tijekom 75 minuta pri vršnu temperaturu od 100°C i tlak od 0,3 MPa u reaktorskoj koloni. U sljedećem koraku, ova se pulpa ubrizgava u bazen i podvrgava ukapljivanju, čime se proizvodi nebijeljena pulpa slame s duljinom loma od 7,2 km, vlačnom čvrstoćom od 45 puta, vlačnom čvrstoćom od 250 mN, svjetlinom od 42% ISO a finoća pulpe 33 °SR.
Predstavljena nebijeljena slamnata masa s masenim udjelom od 50 % i nebijeljena drvena celuloza s masenim udjelom od 50 % najprije se odvojeno melju u cilindričnom pročistaču pri koncentraciji od 3,8 %, tlaku od 0,20 MPa i električnoj struji od 62 A. , zatim u rafineru s dvostrukom pločom pri koncentraciji 3,4%, tlaku 0,20 MPa i električnoj struji 60 A. Standard kvalitete pripremljene pulpe je stupanj mljevenja 48°SR i svježa masa 3,2 g. postojećom tehnologijom, opisana nebijeljena drvna masa se priprema s vlačnom duljinom od 6,5 km, vlačnom čvrstoćom od 1000 mN, stupnjem bjeline 20% ISO, vlačnom čvrstoćom nakon ponovljenog savijanja više od 1000 puta i stupnjem mljevenja 38°SR. Ova celuloza uključuje nebijeljenu sulfatnu celulozu mekog drveta, nebijeljenu sulfitnu celulozu mekog drveta itd.
Za proizvodnju mljevene celuloze za dobivanje fotokopirnog papira prirodne boje, gustoće - 65,0 g / m 2, prosječne duljine loma u uzdužnom i poprečnom smjeru - 7,5 km, uzdužne krutosti savijanja - 82 mN, poprečne krutosti savijanja - 55 mN, stupnja bjeline 41,8% ISO.
Rižina slama, nakon obrade suhom metodom drobilicom čekićem, ulijeva se u kuglasti digestor, gdje se apsolutno suhim sirovinama dodaje otopina reagensa za kuhanje s utroškom lužine u NaOH od 15% i antrakinona od 0,6%, modul kupke 1:3. Smjesa se zagrijava do temperature od 120°C uz vrijeme zadržavanja od 20 minuta, podvrgava laganom oslobađanju plina 20-30 minuta i zagrijava 40 minuta do temperature od 168°C uz vrijeme zadržavanja od 90 minuta. Tvrdoća celuloze nakon kuhanja je 18, što je jednako Kappa broju 27, stupanj mljevenja je 17°SR. Pulpa visoke tvrdoće obrađuje se konvencionalnom prijelaznom jednopužnom prešom dizajniranom za ekstrakciju crne tekućine. Izlazna celuloza se razrijedi do koncentracije 2,5% razrijeđenom crnom otopinom i prosijava vibrirajućim sitom (gubitak celuloze - 0,2%) i čisti sortiranjem od nečistoća (gubitak - 0,1%). Pročišćena celuloza se pere vodoravnom trakom za pranje u koncentraciji od 3,0% i temperaturi od 68-70°C. Nakon toga, izlazna koncentracija doseže do 9%. U sljedećem koraku, pulpa se otapa visokofrekventnim strojem za otapanje, zagrijava se pužom na 70°C nakon koncentriranja i pumpa u cijev za pulpu srednje koncentracije. Ta se celuloza fluidizira toplinskim poboljšanjem (uklanjanjem zraka) u cijevi i pumpa centrifugalnom pumpom u reaktor stupca za delignifikaciju kisika. Celuloza se miješa u cjevovodu do kolonskog reaktora s kisikom (20 kg/t celuloze) i lužnatom otopinom koja sadrži alkalije u NaOH prema težini 4% apsolutno suhe celuloze, zatim se zagrijava parom. Nakon potpunog miješanja celuloze pri ulaznoj temperaturi od 102 °C i tlaku od 1,12 MPa sa zaštitnim reagensom magnezijevim sulfatom pri utrošku od 1% težine apsolutno suhe celuloze, podvrgava se reakciji delignifikacije tijekom 70 minuta pri vršnu temperaturu od 104 °C i tlak od 0,5 MPa u reaktorskoj koloni. U sljedećem koraku, ova se pulpa ubrizgava u bazen i podvrgava ukapljivanju, čime se proizvodi nebijeljena pulpa od slame s duljinom loma od 4,4 km, vlačnom čvrstoćom na višestrukim pregibima od 65 puta, vlačnom čvrstoćom od 245 mN, svjetlinom od 37% ISO i finoća pulpe od 34 °SR.
Maseni udio 70% nebijeljene celuloze stabljike i 30% maseni udio nebijeljene drvene celuloze odvojeno su samljeveni u rafineru s dva diska u koncentraciji od 3,2%, odnosno 4,5%. Standard kvalitete pripremljene celuloze: za celulozu stabljike - stupanj mljevenja 55 ° SR i svježa težina 2,0 g, za drvnu celulozu - 48 ° SR i 2,0 g, respektivno. Predstavljena drvna pulpa je sulfatna pulpa od širokolisnog drveta pripremljena korištenjem postojeće tehnologije.
Obradite mljevenu celulozu za proizvodnju papira za fotokopiranje prirodne boje.
Parametri fotokopirnog papira u prirodnoj boji: gustoća 72,0 g/m2, prosječna prekidna duljina u poprečnom i uzdužnom smjeru 6,2 km, krutost na savijanje 90 mN, krutost na bočno savijanje 56 mN, bjelina 35,0% ISO.
Rižine i pšenične slamke masenog omjera 1:3 obrađuju se drobilicom čekićem suhom metodom, zatim ulaze u digestor, gdje se dodaje otopina reagensa za kuhanje uz potrošnju lužine u NaOH od 11% do apsolutnog suha. sirovina, sulfiditet 5% i modul kupke 1:4. Smjesa se zagrijava na temperaturu od 110°C uz vrijeme zadržavanja od 20 minuta, podvrgava laganom oslobađanju plina 30 minuta i zagrijava 40 minuta do temperature od 168°C uz vrijeme zadržavanja od 90 minuta. Tvrdoća celuloze nakon kuhanja je 19, što je jednako Kappa broju 29, stupanj mljevenja je 14,3°SR. Pulpa visoke tvrdoće obrađuje se konvencionalnom prijelaznom jednopužnom prešom dizajniranom za ekstrakciju crne tekućine. Izlazna celuloza se razrijedi do koncentracije od 3,0% razrijeđenom crnom otopinom i prosije vibrirajućim sitom (gubitak celuloze - 0,2%) i pročisti od nečistoća sortiranjem (gubitak - 0,1%). Pročišćena celuloza je isprana s horizontalnom trakom za ispiranje u koncentraciji od 3,0% i temperaturi od 70°C. Nakon toga, izlazna koncentracija doseže do 9%. U sljedećoj fazi, celuloza se otapa na visokofrekventnom stroju za otapanje, fluidizira u celuloznoj cijevi srednje koncentracije metodom uklanjanja zraka i pumpa centrifugalnom pumpom u reaktor stupca za delignifikaciju kisika. Celuloza se miješa u cjevovodu do kolonskog reaktora s kisikom (20 kg/t celuloze) i lužnatom otopinom koja sadrži alkalije u NaOH prema težini 4% apsolutno suhe celuloze, zatim se zagrijava parom. Nakon potpunog miješanja celuloze pri ulaznoj temperaturi od 95°C i tlaku od 0,9 MPa sa zaštitnim reagensom magnezijevim sulfatom uz utrošak od 1% težine apsolutno suhe celuloze, podvrgava se reakciji delignifikacije tijekom 75 minuta pri vršnu temperaturu od 100°C i tlak od 0,3 MPa u reaktorskoj koloni. U sljedećem koraku, ova se pulpa ubrizgava u bazen i podvrgava ukapljivanju, čime se proizvodi nebijeljena pulpa slame s duljinom loma od 7,2 km, vlačnom čvrstoćom od 45 puta, vlačnom čvrstoćom od 250 mN, svjetlinom od 42% ISO a finoća pulpe 33 °SR.
Nebijeljena slamnata pulpa je mljevena, finoće 30°SR, svježe mase 2,3 g.
Papirnata kutija za hranu u prirodnoj boji dobiva se metodom prerade nakon miješanja mljevene homogene celuloze. Za tretman se koristi ulje-zaštitno sredstvo s volumenom od 1,1%; sredstvo za zaštitu od vode 3,3%, anionski trap za slamke 0,15%, pri vakuumu od 0,055 MPa, temperatura sušenja 180°C, vrijeme sušenja 75 s. Rezultirajuća papirnata kutija za hranu u potpunosti je u skladu sa standardom GB 18006.1-1999 klasa A.
Rižina slama, nakon obrade suhom metodom drobilicom čekićem, ulijeva se u kuglasti digestor, gdje se apsolutno suhim sirovinama dodaje otopina reagensa za kuhanje s utroškom lužine u NaOH od 15% i antrakinona od 0,6%, modul kupke 1:3. Smjesa se zagrijava do temperature od 120°C uz vrijeme zadržavanja od 20 minuta, zatim se podvrgne laganom oslobađanju plina 20-30 minuta i zagrijava 40 minuta do temperature od 168°C uz vrijeme zadržavanja od 90 minuta . Tvrdoća celuloze nakon kuhanja je 18, što je jednako Kappa broju 27, stupanj mljevenja je 17°SR. Pulpa visoke tvrdoće obrađuje se konvencionalnom prijelaznom jednopužnom prešom dizajniranom za ekstrakciju crne tekućine. Izlazna celuloza se razrijedi do koncentracije 2,5% razrijeđenom crnom otopinom i prosijava vibrirajućim sitom (gubitak celuloze - 0,2%) i čisti sortiranjem od nečistoća (gubitak - 0,1%). Pročišćena celuloza se pere vodoravnom trakom za pranje u koncentraciji od 3,0% i temperaturi od 68-70°C. Nakon toga, izlazna koncentracija doseže do 9%. U sljedećem koraku, pulpa se otapa visokofrekventnim strojem za otapanje, zagrijava se pužom na 70°C nakon koncentriranja i pumpa u cijev za pulpu srednje koncentracije. Ta se celuloza fluidizira toplinskim poboljšanjem (uklanjanjem zraka) u cijevi i pumpa centrifugalnom pumpom u reaktor stupca za delignifikaciju kisika. Celuloza se miješa u cjevovodu do kolonskog reaktora s kisikom (20 kg/t celuloze) i lužnatom otopinom koja sadrži alkalije u NaOH prema težini 4% apsolutno suhe celuloze, zatim se zagrijava parom. Nakon potpunog miješanja celuloze pri ulaznoj temperaturi od 102 °C i tlaku od 1,12 MPa sa zaštitnim reagensom magnezijevim sulfatom pri utrošku od 1% težine apsolutno suhe celuloze, podvrgava se reakciji delignifikacije tijekom 70 minuta pri vršnu temperaturu od 104 °C i tlak od 0,5 MPa u reaktorskoj koloni. U sljedećem koraku, ova se pulpa ubrizgava u bazen i podvrgava ukapljivanju, čime se proizvodi nebijeljena pulpa od slame s duljinom loma od 4,4 km, vlačnom čvrstoćom na višestrukim pregibima od 65 puta, vlačnom čvrstoćom od 245 mN, svjetlinom od 37% ISO i finoća pulpe od 34 °SR.
Navedena nebijeljena slamnata masa s masenim udjelom od 70% i nebijeljena drvna masa s masenim udjelom od 30% se melju odvojeno, stupanj mljevenja nebijeljene slamnate celuloze je 31°SR, svježa masa - 2,2 g, drvna masa: 20° SR, svježa težina - 10 g.
Papirnata kutija za hranu u prirodnoj boji dobiva se metodom prerade nakon miješanja mljevene homogene celuloze. Za tretman se koristi ulje-zaštitno sredstvo s volumenom od 1,1%; sredstvo za zaštitu od vode 3,3%, anionski trap za slamke 0,15%, pri vakuumu od 0,05 MPa, temperatura sušenja 178°C, vrijeme sušenja 78 s. Rezultirajuća papirnata kutija za hranu u potpunosti je u skladu sa standardom GB 18006.1-1999 klasa A.
Reed arundo, nakon obrade suhom metodom, ulijeva se u kuglasti digestor, gdje se dodaje otopina reagensa za kuhanje s utroškom lužine (u NaOH) od 11% apsolutno suhih sirovina i utroškom antrakinona od 0,8%, modul kupke 1:4. Smjesa se zagrijava do temperature od 130°C uz vrijeme zadržavanja od 40 minuta, zatim se podvrgne laganom oslobađanju plina tijekom 30 minuta i zagrijava 60 minuta do temperature od 173°C uz vrijeme zadržavanja od 60 minuta. Tvrdoća celuloze nakon kuhanja je 25, što je jednako Kappa broju 45, stupanj mljevenja je 12°SR. Celuloza visoke tvrdoće prerađuje se suvremenom prijelaznom jednopužnom prešom namijenjenom ekstrakciji crne lužine, nakon čega se dobiva celuloza koncentracije 20%, prosijana vibrirajućim sitom (gubitak celuloze - 0,2%) i pročišćena od nečistoća sortiranjem. (gubitak - 0,1%). Pročišćena celuloza se pere vodoravnom trakom za pranje u koncentraciji od 2,0% i temperaturi od 68-70°C. Nakon toga, izlazna koncentracija doseže do 9%. Pulpa se zatim zagrijava na 70°C pomoću pužnice za naknadnu koncentraciju i pumpa u cijev za pulpu srednje koncentracije. Ta se celuloza fluidizira toplinskim poboljšanjem (uklanjanjem zraka) u cijevi i pumpa centrifugalnom pumpom u reaktor stupca za delignifikaciju kisika. Celuloza se miješa u cjevovodu do reaktora na stupcu s kisikom (20 kg/t celuloze) i lužnatom otopinom koja sadrži alkalije (u NaOH) u količini od 4% apsolutno suhe celuloze, zatim se zagrijava parom. Nakon potpunog miješanja celuloze pri ulaznoj temperaturi od 102 °C i tlaku od 1,12 MPa sa zaštitnim reagensom magnezijevim sulfatom pri utrošku od 1% težine apsolutno suhe celuloze, podvrgava se reakciji delignifikacije tijekom 75 minuta pri vršnu temperaturu od 104 °C i tlak od 0,5 MPa u reaktorskoj koloni. U sljedećem koraku, ova se pulpa ubrizgava u bazen i podvrgava ukapljivanju, čime se proizvodi nebijeljena pulpa slame s duljinom loma od 5,0 km, vlačnom čvrstoćom od 69 puta, vlačnom čvrstoćom od 255 mN, svjetlinom od 42% ISO a finoća pulpe 33°SR .
Navedena nebijeljena slamnata masa s masenim udjelom od 70% i nebijeljena drvna masa s masenim udjelom od 30% prvo se posebno melju, stupanj mljevenja nebijeljene slamnate celuloze je 32°SR, svježa masa - 2,3 g, drvna masa: - 20°SR, svježa težina - 12 g.
Papirnata kutija za hranu u prirodnoj boji dobiva se metodom prerade nakon miješanja mljevene homogene celuloze. Za tretiranje se koristi sredstvo za zaštitu ulja s volumenom od 1,2%; vodozaštitno sredstvo 3%, anionski slamčica 0,15%, pri vakuumu od 0,055 MPa, temperatura sušenja 175°C, vrijeme sušenja 80 s.
Rezultirajuća papirnata kutija za hranu u potpunosti je u skladu sa standardom GB 18006.1-1999 klasa A.
Preradite mljevenu pulpu u papirnati ručnik prirodne boje na jednocilindričnom stroju za izradu papira s dugom žicom.
Gustoća papirnatog ručnika prirodne boje je 23,0 g/m2, visina kapilarnog uzdizanja tekućine u poprečnom smjeru je 66 mm/100 s, mokra vlačna čvrstoća u uzdužnom smjeru je 36 N/m, stupanj bjelina je 41,5% ISO.
Nakon pripreme sirovine od rižine slame suhom metodom, koristeći drobilicu čekićem, pretočiti je u kuglasti šaržni digestor, gdje dodati amonijev sulfit uz 13% utroška apsolutno suhe sirovine, modul kupke je 1:4. Smjesa se zagrijava na 120°C 40 minuta, zatim se podvrgne laganom oslobađanju plina 25 minuta i zagrijava 60 minuta na 168°C 90 minuta. Tvrdoća celuloze nakon kuhanja je 16, što je jednako Kappa broju 23, stupanj mljevenja je 23,4°SR. Pulpa se razrjeđuje crnom tekućinom do koncentracije od 2,5% i prosijava pomoću postojeće tehnologije kao što je vibrirajuće sito. Gubitak celuloze u ovom procesu je 0,2%. Operite celulozu vakuumskom strugačom. Nakon toga se vijkom visokotvrda celuloza koncentracije 10% zagrijava na 70°C i transportira u celuloznu cijev srednje koncentracije. Ta se celuloza fluidizira toplinskim poboljšanjem (uklanjanjem zraka) u cijevi i pumpa centrifugalnom pumpom u reaktor stupca za delignifikaciju kisika. Celuloza se miješa u cjevovodu do kolonskog reaktora s kisikom (20 kg/t celuloze) i lužnatom otopinom koja sadrži alkalije u NaOH uz utrošak od 3,5% apsolutno suhe celuloze, zatim se zagrijava parom. Nakon potpunog miješanja, celuloza s ulaznom temperaturom od 95°C i tlakom od 0,9 MPa sa zaštitnim reagensom magnezijevim sulfatom od 1% do apsolutno suhe celuloze podvrgava se reakciji delignifikacije tijekom 75 minuta pri vršnoj temperaturi od 100° C i tlaka od 0,4 MPa u reaktoru u koloni. U sljedećem koraku, ova se pulpa ubrizgava u bazen i podvrgava ukapljivanju, čime se proizvodi nebijeljena pulpa slame s duljinom loma od 6,8 km, vlačnom čvrstoćom od 50 puta, vlačnom čvrstoćom od 250 mN, svjetlinom od 45% ISO a finoća pulpe 36 °SR.
Izvadite mljevenu pulpu nakon potpunog miješanja kako biste dobili papirnati ručnik prirodne boje. Obrada se provodi na dvocilindričnom stroju za proizvodnju papira s dugim očicama. Gustoća papirnatog ručnika prirodne boje je 38,2 g/m2, visina kapilarnog uzdizanja tekućine u poprečnom smjeru je 60 mm/100 s, mokra vlačna čvrstoća u uzdužnom smjeru je 30 N/m, stupanj bjelina je 38% ISO.
Sirovine iz komine šećerne trske pripremaju se općeprihvaćenim suhim postupkom, nakon vađenja jezgre ulijevaju se u kuglasti digestor, gdje se apsolutno suhim sirovinama dodaje 11% otopina reagensa za kuhanje s amonijevim sulfitom, omjer tekućine prema sirovinama je 1:2,5. Smjesa se zagrijava na temperaturu od 130°C uz vrijeme zadržavanja od 20 minuta, podvrgava laganom oslobađanju plina 20 minuta i zagrijava 50 minuta do temperature od 165°C uz vrijeme zadržavanja od 70 minuta. Tvrdoća celuloze nakon kuhanja je 21, što je jednako Kappa broju 32, stupanj mljevenja je 14,2°SR. Pulpa visoke tvrdoće obrađuje se u dvopužnoj preši za crnu lužinu kako bi se povećala koncentracija na 25%, zatim se razrijedi na 2,5% i ispere vakuumskim čistačem. Nakon toga se celuloza koncentracije od 10 do 13 % zagrijava pomoću puža na temperaturu od 70 °C i transportira u celuloznu cijev srednje koncentracije. Ta se celuloza fluidizira toplinskim poboljšanjem (uklanjanjem zraka) u cijevi i pumpa centrifugalnom pumpom u reaktor stupca za delignifikaciju kisika. Celuloza se miješa u cjevovodu do kolonskog reaktora s kisikom (30 kg/t celuloze) i lužnatom otopinom koja sadrži alkalije u NaOH prema težini 3% apsolutno suhe celuloze, zatim se zagrijava parom. Nakon potpunog miješanja celuloze na ulaznoj temperaturi od 98°C i tlaku od 1,05 MPa sa zaštitnim reagensom magnezijevim sulfatom na 0,8% apsolutno suhe celuloze se podvrgava reakciji delignifikacije tijekom 85 minuta na vršnoj temperaturi od 102° C i tlak od 0,4 MPa u reaktorskoj koloni. U sljedećem koraku, ova se pulpa ubrizgava u bazen i podvrgava ukapljivanju, čime se proizvodi nebijeljena pulpa slame s duljinom loma od 6,0 km, vlačnom čvrstoćom na višestrukim savijanjima od 70 puta, vlačnom čvrstoćom od 230 mN, svjetlinom od 40% ISO i finoća pulpe od 35 °SR.
Prikazana nebijeljena slamnata pulpa s masenim udjelom od 80 % i nebijeljena drvna pulpa s masenim udjelom od 20 % melju se odvojeno pri koncentraciji od 3,2 % odnosno 4,0 %, mljevenje se provodi sekvencijalno u dvocilindričnom rafineru a u rafineru s dva diska. Standard kvalitete pripremljene celuloze: za slamu - stupanj mljevenja 50 ° SR i mokre težine 1,8 g, za lisnato drvo - 41 ° SR, odnosno 1,5 g. Postojeća tehnologija proizvodi nebijeljenu drvnu pulpu s duljinom loma od 4,5 km, vlačnom čvrstoćom od 500 mN, svjetlinom od 18% ISO, vlačnom čvrstoćom od više od 1000 puta i slobodnošću od 38°SR. Ova celuloza uključuje nebijeljenu sulfatnu celulozu mekog drveta, nebijeljenu sulfitnu celulozu mekog drveta itd.
Izvadite mljevenu pulpu nakon potpunog miješanja kako biste dobili papirnati ručnik prirodne boje. Dorada se izvodi na jednocilindričnom stroju za kosi papir. Parametri navedenog papirnatog ručnika prirodne boje: gustoća - 45,0 g/m2, visina kapilarnog dizanja tekućine u poprečnom smjeru - 55 mm/100 s, vlačna čvrstoća u mokrom stanju u uzdužnom smjeru - 28 N/m, stupanj bjeline - 41 % ISO.
Rižina slama, nakon obrade suhom metodom drobilicom čekićem, ulijeva se u kuglasti digestor, gdje se potpuno suhoj sirovini dodaje otopina reagensa za kuhanje s udjelom lužine (u NaOH) od 15% i antrakinona od 0,6%. materijala, modul kupke 1:3. Smjesa se zagrijava do temperature od 120°C uz vrijeme zadržavanja od 20 minuta, podvrgava laganom oslobađanju plina 20-30 minuta i zagrijava 40 minuta do temperature od 168°C uz vrijeme zadržavanja od 90 minuta. Tvrdoća celuloze nakon kuhanja je 18, što je jednako Kappa broju 27, stupanj mljevenja je 17°SR. Pulpa visoke tvrdoće obrađuje se konvencionalnom prijelaznom jednopužnom prešom dizajniranom za ekstrakciju crne tekućine. Izlazna celuloza se razrijedi do koncentracije 2,5% razrijeđenom crnom otopinom i prosijava vibrirajućim sitom (gubitak celuloze - 0,2%) i čisti sortiranjem od nečistoća (gubitak - 0,1%). Pročišćena celuloza se pere vodoravnom trakom za pranje u koncentraciji od 3,0% i temperaturi od 68-70°C. Nakon toga, izlazna koncentracija doseže do 9%. U sljedećem koraku, pulpa se otapa visokofrekventnim strojem za otapanje, zagrijava se pužom na 70°C nakon koncentriranja i pumpa u cijev za pulpu srednje koncentracije. Ta se celuloza fluidizira toplinskim poboljšanjem (uklanjanjem zraka) u cijevi i pumpa centrifugalnom pumpom u reaktor stupca za delignifikaciju kisika. Celuloza se miješa u cjevovodu do kolonskog reaktora s kisikom (20 kg/t celuloze) i lužnatom otopinom koja sadrži alkalije u NaOH prema težini 4% apsolutno suhe celuloze, zatim se zagrijava parom. Nakon potpunog miješanja celuloze pri ulaznoj temperaturi od 102 °C i tlaku od 1,12 MPa sa zaštitnim reagensom magnezijevim sulfatom pri utrošku od 1% težine apsolutno suhe celuloze, podvrgava se reakciji delignifikacije tijekom 70 minuta pri vršnu temperaturu od 104 °C i tlak od 0,5 MPa u reaktorskoj koloni. U sljedećem koraku, ova se pulpa ubrizgava u bazen i podvrgava ukapljivanju, čime se proizvodi nebijeljena pulpa slame s duljinom loma od 4,4 km, vlačnom čvrstoćom od 65 puta, vlačnom čvrstoćom od 245 mN, svjetlinom od 37% ISO a finoća pulpe 34 °SR.
95% masenog udjela nebijeljene celuloze stabljike i 5% masenog udjela nebijeljene drvene pulpe odvojeno su samljevene u rafineru s dva diska u koncentraciji od 3,2% odnosno 4,5%. Standard kvalitete pripremljene celuloze: za celulozu stabljike - stupanj mljevenja 55 ° SR i svježa težina 2,0 g, za drvnu celulozu - 48 ° SR i 2,0 g, respektivno. Predstavljena drvna pulpa je sulfatna pulpa od širokolisnog drveta pripremljena korištenjem postojeće tehnologije.
Ekstrahirajte mljevenu pulpu nakon potpunog miješanja kako biste proizveli papirnati papir prirodne boje.
Parametri navedenog sanitarnog papira prirodne boje: gustoća 18,0 g/m2, visina kapilarnog dizanja tekućine u poprečnom smjeru 60 mm/100 s, vlačna čvrstoća - 7,0 N m/g, mekoća - 130 mN, stupanj bjeline - 50 % ISO.
Reed arundo, nakon obrade suhom metodom, ulijeva se u kuglasti digestor, gdje se dodaje otopina reagensa za kuhanje s utroškom lužine (u NaOH) od 11% apsolutno suhih sirovina i utroškom antrakinona od 0,8%, modul kupke 1:4. Smjesa se zagrijava do temperature od 130°C uz vrijeme zadržavanja od 40 minuta, zatim se podvrgne laganom oslobađanju plina tijekom 30 minuta i zagrijava 60 minuta do temperature od 173°C uz vrijeme zadržavanja od 60 minuta. Tvrdoća celuloze nakon kuhanja je 25, što je jednako Kappa broju 45, stupanj mljevenja je 12°SR. Celuloza visoke tvrdoće prerađuje se suvremenom prijelaznom jednopužnom prešom namijenjenom ekstrakciji crne lužine, nakon čega se dobiva celuloza koncentracije 20%, prosijana vibrirajućim sitom (gubitak celuloze - 0,2%) i pročišćena od nečistoća sortiranjem. (gubitak - 0,1%). Pročišćena celuloza se pere vodoravnom trakom za pranje u koncentraciji od 2,0% i temperaturi od 68-70°C. Nakon toga, izlazna koncentracija doseže do 9%. Pulpa se zatim zagrijava na 70°C pomoću pužnice za naknadnu koncentraciju i pumpa u cijev za pulpu srednje koncentracije. Ta se celuloza fluidizira toplinskim poboljšanjem (uklanjanjem zraka) u cijevi i pumpa centrifugalnom pumpom u reaktor stupca za delignifikaciju kisika. Celuloza se miješa u cjevovodu do reaktora na stupcu s kisikom (20 kg/t celuloze) i lužnatom otopinom koja sadrži alkalije (u NaOH) u količini od 4% apsolutno suhe celuloze, zatim se zagrijava parom. Nakon potpunog miješanja celuloze pri ulaznoj temperaturi od 102 °C i tlaku od 1,12 MPa sa zaštitnim reagensom magnezijevim sulfatom pri utrošku od 1% težine apsolutno suhe celuloze, podvrgava se reakciji delignifikacije tijekom 75 minuta pri vršnu temperaturu od 104 °C i tlak od 0,5 MPa u reaktorskoj koloni. U sljedećem koraku, ova se pulpa ubrizgava u bazen i podvrgava ukapljivanju, čime se proizvodi nebijeljena pulpa slame s duljinom loma od 5,0 km, vlačnom čvrstoćom od 69 puta, vlačnom čvrstoćom od 255 mN, svjetlinom od 42% ISO a finoća pulpe 33 °SR.
Predstavljena nebijeljena slamnata masa s masenim udjelom od 70% i nebijeljena drvena celuloza s masenim udjelom od 30% prvo se odvojeno melju u cilindričnom rafineru pri koncentraciji od 3,8%, tlaku od 0,15-0,20 MPa i električnoj struji od 65 A, zatim u rafineru s dvostrukom pločom pri koncentraciji 3 ,3 %, tlaku 0,20 MPa i električnoj struji 60 A, dok se ne steknu uvjeti da je stupanj rafinacije pulpe 48°SR i svježa težina je 2,8 g. Primjenom postojeće tehnologije pripremljena je navedena nebijeljena drvna masa duljine loma 6 km, vlačne čvrstoće 1000 mN, 18% ISO svjetline, 1000+ čvrstoće na savijanje i 40°SR stupnja mljevenja. Ova celuloza uključuje nebijeljenu sulfitnu celulozu širokog lista, nebijeljenu sulfitnu celulozu mekog drveta, itd.
Parametri navedenog sanitarnog papira prirodne boje: gustoća 11,0 g/m2, visina kapilarnog izdizanja tekućine u poprečnom smjeru - 80 mm/100 s, vlačna čvrstoća - 10,0 N m/g, mekoća - 120 mN, stupanj bjeline. - 38% ISO.
Rižina slama, slama pšenice i trske masenog omjera 1:3:1 prerađuju se suhom metodom drobilicom čekićem i utovaruju u digestor, zatim uz pomoć vruće crne luge na temperaturi od 135°C ulaze u digestor kroz otvor za punjenje, dok se modul kupelji postiže na 1:8. Zatvorite poklopac kotla prilikom punjenja, dodajte otopinu reagensa za kuhanje u kotao na temperaturi od 145 ° C uz potrošnju lužine u NaOH od 11% do apsolutno suhih sirovina, antrakinon - 0,8%. Uklonite crnu tekućinu i zrak i povećajte tlak na 0,6 MPa. Zatim uključite recirkulacijsku crpku kotla i cijevni grijač kako biste povećali temperaturu otopine reagensa za kuhanje na 160°C. Porast temperature i izloženost traju samo 180 minuta. Vruća crna tekućina zamjenjuje se razrijeđenom tekućinom i transportira u spremnik vruće crne tekućine. Tvrdoća dobivene celuloze nakon kuhanja je 19, što je jednako Kappa broju 29, stupanj mljevenja je 16°SR. Pulpa visoke tvrdoće obrađuje se konvencionalnom prijelaznom jednopužnom prešom dizajniranom za ekstrakciju crne tekućine. Izlazna celuloza se razrijedi do koncentracije od 3,0% razrijeđenom crnom otopinom i prosije vibrirajućim sitom (gubitak celuloze - 0,2%) i pročisti od nečistoća sortiranjem (gubitak - 0,1%). Pročišćena celuloza je isprana s horizontalnom trakom za ispiranje u koncentraciji od 3,0% i temperaturi od 70°C. Nakon toga, izlazna koncentracija doseže do 9%. U sljedećoj fazi, celuloza se otapa na visokofrekventnom stroju za otapanje, fluidizira u celuloznoj cijevi srednje koncentracije metodom uklanjanja zraka i pumpa centrifugalnom pumpom u reaktor stupca za delignifikaciju kisika. Celuloza se miješa u cjevovodu do kolonskog reaktora s kisikom (20 kg/t celuloze) i lužnatom otopinom koja sadrži alkalije u NaOH prema težini 4% apsolutno suhe celuloze, zatim se zagrijava parom. Nakon potpunog miješanja celuloze pri ulaznoj temperaturi od 95°C i tlaku od 0,9 MPa sa zaštitnim reagensom magnezijevim sulfatom uz utrošak od 1% težine apsolutno suhe celuloze, podvrgava se reakciji delignifikacije tijekom 75 minuta pri vršnu temperaturu od 100°C i tlak od 0,4 MPa u reaktorskoj koloni. U sljedećem koraku, ova se pulpa ubrizgava u bazen i podvrgava ukapljivanju, čime se proizvodi nebijeljena pulpa slame s duljinom loma od 6,5 km, vlačnom čvrstoćom od 45 puta, vlačnom čvrstoćom od 250 mN, svjetlinom od 42% ISO i finoćom celuloza - 33°SR.
95% nebijeljene slamnate pulpe i 5% nebijeljene drvene pulpe odvojeno se melje u rafineru s dva diska u koncentraciji od 3,4%. Standard kvalitete pripremljene pulpe je: stupanj mljevenja 48°SR i svježa masa 2,9 g. Koristeći postojeću tehnologiju, prezentirana nebijeljena drvna pulpa se priprema s duljinom loma od 6 km, vlačnom čvrstoćom 1000 mN, stupnjem svjetline 20% ISO, vlačna čvrstoća kod ponovljenih savijanja više od 1000 puta i stupanj brušenja 38°SR. Ova celuloza uključuje nebijeljenu sulfitnu celulozu širokog lista, nebijeljenu sulfitnu celulozu mekog drveta, itd.
Obradite mljevenu celulozu kako biste proizveli svileni papir prirodne boje.
Parametri navedenog sanitarnog papira prirodne boje: gustoća - 13,0 g/m 2, visina kapilarnog dizanja tekućine u poprečnom smjeru - 30 mm/100 s, vlačna čvrstoća u mokrom stanju u uzdužnom smjeru - 22 N/m , mekoća - 140 mN, svjetlina - 50% ISO.
Pšenična slama se obrađuje drobilicom čekićem, zatim se puni u digestor, gdje se dodaje otopina reagensa za kuhanje s amonijevim sulfitom u 9% utroška apsolutno suhe sirovine, kupeljni modul 1:3. Smjesa se zagrijava do 110°C 30 minuta, zatim se podvrgne laganom oslobađanju plina 25 minuta i zagrijava 60 minuta do temperature od 168°C 90 minuta. Tvrdoća celuloze nakon kuhanja je 22, što je jednako Kappa broju 35,5, stupanj mljevenja je 11,6°SR. Pulpa se razrjeđuje crnom tekućinom do koncentracije od 2,5% i prosijava pomoću postojeće tehnologije kao što je vibrirajuće sito. Gubitak celuloze u ovom procesu je 0,5%. Operite celulozu vakuumskom strugačom. Nakon pranja dobiva se visokotvrda celuloza koncentracije 10%, koja se šalje u celuloznu cijev srednje koncentracije i pumpa u kolonu reaktora za delignifikaciju kisikom. Celuloza se miješa u cjevovodu do reaktora na stupcu s kisikom (20 kg/t celuloze) i lužnatom otopinom koja sadrži alkalije (u NaOH) u količini od 4% apsolutno suhe celuloze, zatim se zagrijava parom. Nakon potpunog miješanja, celuloza s ulaznom temperaturom od 95°C i tlakom od 0,9 MPa sa zaštitnim reagensom magnezijevim sulfatom od 1% do apsolutno suhe celuloze podvrgava se reakciji delignifikacije tijekom 75 minuta pri vršnoj temperaturi od 100° C i tlaka od 0,3 MPa u reaktoru u koloni. U sljedećem koraku, ova se pulpa ubrizgava u bazen i podvrgava ukapljivanju, čime se proizvodi nebijeljena pulpa slame s duljinom loma od 5,0 km, vlačnom čvrstoćom od 40 puta, vlačnom čvrstoćom od 220 mN, svjetlinom od 40% ISO a finoća pulpe 34 °SR. Nebijeljena pulpa slame podvrgava se mljevenju, kriterij dobivene pulpe je: stupanj mljevenja 45°SR, svježa masa 2,8 g.
Obradite mljevenu celulozu za proizvodnju kućanskog papira prirodne boje. Dorada se izvodi na dugoliničnom jednocilindričnom stroju za izradu papira.
Parametri navedenog kućanskog papira prirodne boje: gustoća 14,0 g/m 2, visina kapilarnog dizanja tekućine u poprečnom smjeru - 100 mm/100 s, vlačna čvrstoća u mokrom stanju u uzdužnom smjeru - 55 N/m, stupanj bjeline - 45% ISO.
Nakon pripreme sirovine od rižine slame suhom metodom, koristeći drobilicu čekićem, pretočiti je u kuglasti šaržni digestor, gdje dodati amonijev sulfit uz 13% utroška apsolutno suhe sirovine, modul kupke je 1:4. Smjesa se zagrijava na 120°C 40 minuta, zatim se podvrgne laganom oslobađanju plina 25 minuta i zagrijava 60 minuta na 168°C 90 minuta. Tvrdoća celuloze nakon kuhanja je 16, što je jednako Kappa broju 23, stupanj mljevenja je 23,4°SR. Pulpa se razrjeđuje crnom tekućinom do koncentracije od 2,5% i prosijava pomoću postojeće tehnologije kao što je vibrirajuće sito. Gubitak celuloze u ovom procesu je 0,2%. Operite celulozu vakuumskom strugačom. Nakon toga se vijkom visokotvrda celuloza koncentracije 10% zagrijava na 70°C i transportira u celuloznu cijev srednje koncentracije. Ta se celuloza fluidizira toplinskim poboljšanjem (uklanjanjem zraka) u cijevi i pumpa centrifugalnom pumpom u reaktor stupca za delignifikaciju kisika. Celuloza se miješa u cjevovodu do kolonskog reaktora s kisikom (20 kg/t celuloze) i lužnatom otopinom koja sadrži alkalije u NaOH uz utrošak od 3,5% apsolutno suhe celuloze, zatim se zagrijava parom. Nakon potpunog miješanja, celuloza s ulaznom temperaturom od 95°C i tlakom od 0,9 MPa sa zaštitnim reagensom magnezijevim sulfatom od 1% do apsolutno suhe celuloze podvrgava se reakciji delignifikacije tijekom 75 minuta pri vršnoj temperaturi od 100° C i tlaka od 0,4 MPa u reaktoru u koloni. U sljedećem koraku, ova se pulpa ubrizgava u bazen i podvrgava ukapljivanju, čime se proizvodi nebijeljena pulpa slame s duljinom loma od 6,8 km, vlačnom čvrstoćom 50 puta, vlačnom čvrstoćom 250 mN, svjetlinom 45% ISO i finoćom celuloze - 36 °SR.
70% masenog udjela nebijeljene slamnate pulpe i 30% masenog udjela nebijeljene drvene pulpe odvojeno je samljeveno u rafineru s dva diska u koncentraciji od 3,0% odnosno 4,5%. Standard kvalitete pripremljene celuloze: za slamu - stupanj mljevenja 50 ° SR i mokre težine 1,8 g, za drvnu pulpu - 46 ° SR i 1,2 g, respektivno. Duljina loma nebijeljene pulpe širokolisnog drveta je 6,5 km, vlačna čvrstoća je 1000 mN, svjetlina je 18% ISO, čvrstoća loma je 1000 puta, a stupanj rafinacije pulpe je 38°SR.
Ekstrahirajte mljevenu pulpu nakon potpunog miješanja kako biste proizveli papir za kućanstvo prirodne boje. Obrada se provodi na dvocilindričnom stroju za proizvodnju papira s dugim očicama. Parametri navedenog kućanskog papira prirodne boje: gustoća 36,0 g/m2, visina kapilarnog izdizanja tekućine u poprečnom smjeru 60 mm/100 s, vlačna čvrstoća u mokrom stanju u uzdužnom smjeru - 40 N/m, stupanj bjelina - 45 % ISO.
1. Papirni proizvod prirodne boje od sirovine nebijeljene celuloze iz slame žitarica, čija je bjelina 35-60% ISO, karakteriziran time što se za njegovu proizvodnju koristi nebijeljena slamnata celuloza vlačne čvrstoće 230-280 mN, vlačna čvrstoća kod ponovljenih savijanja od 40 -90 puta i permanganatni broj 16-28.
2. Proizvod prema zahtjevu 1, naznačen time, da je duljina loma navedene nebijeljene pulpe slame 5,0 - 7,5 km, bjelina je 25-45% ISO, stupanj rafinacije pulpe je 32-38°SR, poželjno duljina loma od rečena nebijeljena slamnata celuloza - 6,5-7,5 km, bjelina - 35-45% ISO, stupanj mljevenja celuloze - 32-36°SR, vlačna čvrstoća - 250-280 mN.
3. Proizvod u skladu s patentnim zahtjevom 1, koji uključuje papirnu maramicu u prirodnoj boji, papirnati ručnik u prirodnoj boji, papir za brisanje u prirodnoj boji, fotokopirni papir u prirodnoj boji, kutiju za hranu od papira u prirodnoj boji, papir za umatanje hrane u prirodnoj boji i papir za tiskanje u prirodnim bojama.
4. Proizvod prema bilo kojem od zahtjeva 1 do 3, koji je papirnati ubrus prirodne boje koji sadrži 70-100% nebijeljene slamnate pulpe i 0-30% nebijeljene drvene pulpe, ili je papirnati ručnik prirodne boje koji sadrži 70-100% nebijeljene slamnate pulpe i 0-30% nebijeljene drvene pulpe, ili je papir za kutije za hranu u prirodnoj boji napravljen od 70-100% nebijeljene slamnate pulpe i 0-30% nebijeljene drvene pulpe, ili je fotokopirni papir u prirodnoj boji koji sadrži 50-80% nebijeljene slamnate pulpe i 20-50% nebijeljene drvene pulpe, ili je papir za omatanje hrane koji sadrži 50-70% nebijeljene slamnate pulpe i 30-50% nebijeljene drvene pulpe, ili je ofsetni papir u prirodnoj boji koji sadrži 65-85% nebijeljene slamnate pulpe i 15-35% nebijeljene drvene pulpe, ili je papir za brisanje koji sadrži 70-100% nebijeljene slamnate pulpe i 0-30% nebijeljene drvene pulpe.
5. Proizvod prema zahtjevu 4, naznačen time, da je visina kapilarnog dizanja tekućine u poprečnom smjeru svilenog papira prirodne boje 30-100 mm/100 s, poželjno 40-100 mm/100 s, poželjnije 50 -80 mm/100 c, mokra vlačna čvrstoća u uzdužnom smjeru papirnatog ručnika prirodne boje je 22-55 N/m, poželjno 30-45 N/m, ili prosječna duljina kidanja u uzdužnom i poprečnom smjeru prirodne boje papira za fotokopiranje je 3,2-7,5 km, po mogućnosti 4,5-7,5 km, poželjnije 6,0-7,5 km, ili duljina loma prirodnog papira za pakiranje hrane je 3,2-7,6 km, po mogućnosti 4,5-7,6 km, ili duljina loma prirodnog ofsetni papir u boji ovog izuma je 2,5-5,5 km, poželjno 3,5-5,5 km, ili mokra vlačna čvrstoća u uzdužnom smjeru papira za brisanje prirodne boje navedena u ovom izumu je 22-55 N/m, poželjno 30- 45 N/m.
6. Proizvod prema zahtjevu 4, naznačen time, da je vlačna čvrstoća prirodno obojenog svilenog papira 4-12 Nm/g, poželjno 8-12 Nm/g, ili visina kapilarnog dizanja tekućine u poprečnom smjeru papira. prirodna boja ručnika je 30-100 mm/100 s, poželjno 40-100 mm/100 s, poželjnije 50-80 mm/100 s; ili je vlačna čvrstoća kada se opetovano savija u poprečnom smjeru fotokopirnog papira u prirodnoj boji 60-200 puta, poželjno 80-185 puta; ili neprozirnost fotokopirnog papira u prirodnoj boji je 82,0-98,0%, po mogućnosti 90-98%, ili čvrstoća poprečnog savijanja papira za omatanje hrane u prirodnoj boji je 90-200 puta, po mogućnosti 120-200 puta, ili neprozirnost prirodne boje ofsetni papir je 82-98%, po mogućnosti 85-98%, poželjnije 92-98%, ili visina kapilarnog porasta tekućine u poprečnom smjeru papira za brisanje prirodne boje je 30-100 mm/100 s, po mogućnosti 40-100 mm/100 s, poželjnije 50-80 mm/100 s.
7. Proizvod prema zahtjevu 5 ili 6, naznačen time što je mekoća položenog prirodno obojenog papirnatog papira 120-180 mN, poželjno 120-150 mN, ili je mekoća položenog prirodno obojenog papirnatog ručnika 120-180 mN, po mogućnosti 120 -150 mN, ili poprečna vlačna čvrstoća položenog papira za omatanje u prirodnoj boji za hranu je 300-600 mN, poželjno 400-600 mN, ili poprečna vlačna čvrstoća položenog ofsetnog papira u prirodnoj boji je 10-35 puta, po mogućnosti 15 -35 puta.
8. Proizvod prema zahtjevu 5 ili 6, naznačen time, da je gustoća postavljenog papira 10,0-18,0 g/m2, ponajprije 11,0-13,0 g/m2, ili je gustoća postavljenog papirnatog ručnika prirodne boje 23,0 -45,0 g/m2, poželjno 30,0-40,0 g/m2, ili je gustoća postavljenog papira za fotokopiranje u prirodnoj boji 60,0-80,0 g/m2, poželjno 70,0-80,0 g/m2, poželjnije 69,0-72,0 g/m2, ili je gustoća postavljenog papira za pakiranje hrane u prirodnoj boji 45-65 g/m2, po mogućnosti 50-60 g/m2, ili je gustoća papira u prirodnoj boji položenog za brisanje 14,0-36,0 g/m2, po mogućnosti 18 -28 g/m2, odnosno gustoća postavljenog offset papira u prirodnoj boji je 50-70 g/m2, poželjno 60,0 -70,0 g/m2.
9. Proizvod prema zahtjevu 5 ili 6, naznačen time, da je mekoća papira za brisanje prirodne boje 120-200 mN, poželjno 120-180 mN.
10. Proizvod prema bilo kojem od zahtjeva 1-3, naznačen time, da proizvodnja opisane nebijeljene slamnate pulpe uključuje kuhanje i pranje, uklj. dobivanje slamnate celuloze visoke tvrdoće s permanganatnim brojem 16-23 i stupnjem mljevenja 10-24°SR.
11. Proizvod prema bilo kojem od zahtjeva 1-3, naznačen time, da faza proizvodnje nebijeljene slamnate pulpe uključuje kuhanje i delignifikaciju kisikom, uklj. pumpanje visokotvrde celuloze s permanganatnim brojem 16-28 u reaktor-kolonu za delignifikaciju kisikom uz dodatak lužina i kisika i nakon te reakcije dobivanje celuloze s permanganatnim brojem 10-14, dok je odabrana delignifikacija kisikom jednostupanjska reakcija, njezina reakcija se provodi u reaktoru-koloni za delignifikaciju kisikom, temperatura i tlak predstavljene celuloze visoke tvrdoće na ulazu u ovaj kolonski reaktor su 95-100°C i 0,9-1,2 MPa, pri izlaz - 100-105 ° C i 0,2-0,6 MPa, au procesu delignifikacije kisikom, potrošnja lužine u NaOH je 2-4% potrošnje apsolutno suhe celuloze, potrošnja kisika je 20-40 kg za 1 tona apsolutno suhe celuloze, trajanje reakcije je 60-90 minuta.
12. Proizvod prema zahtjevu 10, naznačen time, da postupak kuhanja pulpe uključuje jednu od sljedećih metoda: metodu amonijevog sulfita, antrahion-natrijevu metodu, sulfatnu metodu ili metodu natrijevog sulfita, dok kod kuhanja pomoću amonijevog sulfita metoda, potrošnja amonijevog sulfita je 9-13% potrošnje apsolutno suhih sirovina, pri kuhanju antrakinon-natrijevom metodom, potrošnja NaOH lužine je 9-15% potrošnje apsolutno suhih sirovina, kada kuhanje sulfatnom metodom, potrošnja NaOH lužine je 8-11% potrošnje apsolutno suhih sirovina, pri kuhanju U metodi natrijevog sulfita, potrošnja kaustične kiseline je 11-15% težine apsolutno suhih sirovina , potrošnja natrijevog sulfita je 2-6% težine apsolutno suhih sirovina.
13. Proizvod u skladu s patentnim zahtjevom 12, naznačen time, da postupak izrade pulpe uključuje jednu od sljedećih metoda: metodu s amonijevim sulfitom, antrakino-natrijevu metodu, sulfatnu metodu ili metodu s natrijevim sulfitom, pri čemu se pulpa kuha u sferičnoj šarži. digestor i kontinuirani digestor, metoda amonijevog sulfita uključuje: dodavanje otopine reagensa za kuhanje pulpe biljnim sirovinama žitarica, uklj. potrošnja amonijevog sulfita je 9-13% potrošnje apsolutno suhih sirovina, potrošnja kaustika je 0-8% potrošnje apsolutno suhih sirovina, modul kupelji 1: 2-4, zagrijavanje smjese vodenom parom do temperature od 165-173 ° C s blagim povećanjem temperature otpuštanjem plina i zadržavanjem topline 160-210 minuta, metoda antrahion-natrija uključuje: dodavanje otopine reagensa za kuhanje pulpe biljnim sirovinama žitarica, uklj. Potrošnja lužine u NaOH je 9-15% potrošnje apsolutno suhih sirovina, modul kupatila je 1: 2-4, a potrošnja antrakinona je 0,5-0,8% potrošnje apsolutno suhih sirovina, zagrijavajući smjesu vodenom parom do temperatura od 160-165 °C, porast temperature, lagano oslobađanje plina i zadržavanje topline traju samo 140-190 minuta, opisana sulfatna metoda uključuje: dodavanje otopine reagensa za pulpiranje biljnim sirovinama žitarica, uklj. potrošnja lužine u NaOH je 8-11% potrošnje apsolutno suhih sirovina, modul kupke 1: 2-4, sulfidnost 5-8%; zagrijavanje smjese vodenom parom na temperaturu od 165-173°C, povećanje temperature, lagano oslobađanje plina i zadržavanje topline traje samo 150-200 minuta; Opisana metoda natrijevog sulfita uključuje: dodavanje otopine reagensa za kuhanje celuloze biljnim sirovinama žitarica, uklj. Potrošnja NaOH je 9-15% od težine apsolutno suhih sirovina, potrošnja natrijevog sulfita je 2-6% od težine apsolutno suhih sirovina, potrošnja antrakinona je 0,04-0,08% od potrošnje apsolutno suhih sirovina, kupka modul 1: 3-4 , zagrijavanje smjese vodenom parom na temperaturu od 160-165 °C, povećanje temperature, lagano oslobađanje plina i zadržavanje topline traje samo 140-190 minuta, pri kuhanju u vertikalnom digestoru: sa sulfitom- amonijeva metoda, biljne sirovine žitarica pomoću vruće crne alkalne otopine na temperaturi od 120 -140°C uvode se u digestor kroz otvor za punjenje, nakon punjenja kotao se zatvara poklopcem, reagens za kuhanje na temperaturi od 130°C. U njega se ulijeva -160°C, istovremeno se ispumpava zrak iz kotla i povećava tlak na 0,6-0,75 MPa, a temperatura reagensa za kuhanje na 156-173°C pomoću cirkulacijske pumpe grijanja i cijevni grijač, povećanje temperature, održavanje topline i zamjena traje 180-220 minuta, nakon čega se celuloza upumpava u kotao za ispuhivanje, u zadanoj otopini reagensa za kuhanje pulpe, utrošak amonijevog sulfita je 9-15% potrošnje apsolutno suhih sirovina, potrošnja kaustične sode je 0-8% potrošnje apsolutno suhih sirovina, modul kupke je 1: 6-10, s antrahion-natrijevom metodom, biljnim sirovinama žitarica vruća crna alkalna otopina na temperaturi od 120-140°C uvodi se u digestor kroz otvor za punjenje, nakon punjenja kotao se zatvara poklopcem, u njega se ulijeva reagens za kuhanje na temperaturi od 130-160°C , u isto vrijeme zrak se ispumpava iz kotla i povećava tlak na 0,4-0,6 MPa, a temperatura reagensa za kuhanje na 147-165°C pomoću cirkulacijske pumpe grijanja i cijevnog grijača, podižući temperatura, održavanje topline i zamjena nastavljaju se 180 minuta, nakon čega se celuloza upumpava u kotao za ispuhivanje; u danoj otopini reagensa za pulpiranje, potrošnja lužine NaOH je 9 -17% potrošnje apsolutno suhih sirovina , modul kupatila 1:6-9, potrošnja antrakinona 0,5-0,8%, uz sulfatnu metodu, biljne sirovine žitarica uvode se u digestor pomoću vruće crne alkalne otopine na temperaturi od 120-140 ° C kroz otvor za punjenje, nakon punjenja zatvoriti kotao poklopcem, uliti reagens za kuhanje na temperaturi od 130-160°C, istovremeno ispumpati zrak iz kotla i povećati tlak na 0,5-0,65 MPa, a temperaturu reagensa za kuhanje na 155-168°C pomoću cirkulacijske pumpe za grijanje i cjevastog grijača, povećanje temperature, zadržavanje topline i zamjena nastavljaju se 200-250 minuta, nakon čega se celuloza pumpa u kotao za ispuhivanje, u otopina reagensa za kuhanje pulpe, potrošnja NaOH lužine je 8-13% potrošnje apsolutno suhe sirovine, modul kupelji 1:6-10, sulfidnost 5-9%; metodom natrijevog sulfita, biljne sirovine žitarica uvode se u digestor s vrućom crnom alkalnom otopinom na temperaturi od 120-140 °C kroz otvor za punjenje, nakon punjenja kotao se zatvara poklopcem, reagens za kuhanje na temperature 130-160°C ulijeva se u njega, a zrak se istovremeno ispumpava iz kotla i povećava tlak na 0,45-0,6 MPa, a temperatura reagensa za kuhanje na 152-165°C pomoću cirkulacijske pumpe grijanja i cjevasti grijač., povećavajući temperaturu
14. Proizvod prema zahtjevu 11, naznačen time, da se za pripremu navedene nebijeljene slamnate pulpe, prije kuhanja i delignifikacije kisikom, provodi pranje, uključujući:
(1) pumpanje pulpe visoke tvrdoće koncentracije 8-15% u prešu, cijeđenje crne tekućine iz pulpe i dobivanje proizvoda koncentracije 18-25%, dok je prijelazna preša, jednopužna, dvopužna ili dvostruki valjak koristi se kao preša,
(2) za pranje celuloze nakon cijeđenja u vakuumskom peraču, tlačnom peraču ili vodoravnom trakastom peraču koristite crnu tekućinu s koncentracijom od 3-6,2 ° Be" i pH vrijednošću od 8-8,3 na temperaturi od 70- 80°C, ili temperatura vode 70-80°C, ili crna tekućina i voda.
15. Proizvod u skladu s bilo kojim od patentnih zahtjeva 1-3, naznačen time, da sirovina iz biljaka žitarica uključuje jedan ili više od sljedećih materijala: slamu riže, slamu pšenice, stabljike pamuka, trsku šećerne trske, običnu trsku ili arunda trsku.
16. Metoda za proizvodnju proizvoda od papira prirodne boje prema bilo kojem od zahtjeva 1 do 15, naznačena time što uključuje:
(1) dobivanje navedene nebijeljene pulpe slame uzastopno kuhanjem, pranjem, lomljenjem i delignifikacijom kisikom sirovog materijala iz usjeva žitarica,
(2) naknadno miješanje gornje nebijeljene slamnate pulpe s drvenom pulpom,
(3) ravnomjerno miješanje nebijeljene slamnate pulpe s nebijeljenom drvenom pulpom u koraku (2) prema traženom masenom udjelu pulpe za proizvode od papira,
(4) proizvodnju od dobivene pulpe specificiranih proizvoda od papira prirodne boje, pri čemu se korak kuhanja sastoji od dobivanja slamnate pulpe visoke tvrdoće s permanganatnim brojem od 16-28 i stupnjem mljevenja od 10-24°SR nakon kuhanja sirovog materijala iz usjeva žitarica, po mogućnosti proizvodeći navedenu pulpu slame visoke tvrdoće s permanganatnim brojem 16-23 i stupnjem mljevenja 10-24°SR, faza delignifikacije kisikom uključuje pumpanje visokotvrde celuloze s permanganatnim brojem 16- 28 u stupac reaktora za delignifikaciju kisikom, dodavanjem lužine i kisika, a nakon te reakcije dobivanjem celuloze s permanganatnim brojem 10-14.
0 ,9-1,2 MPa i 100-105°C, 0,2-0,6 MPa, u procesu delignifikacije kisikom, potrošnja alkalnog NaOH je 2-4% potrošnje apsolutno suhe celuloze, potrošnja kisika je 20-40 kg /t apsolutno suhe celuloze, vrijeme reakcije 60-90 min.
18. Metoda u skladu s patentnim zahtjevom 16, naznačena time, da dalje uključuje korak cijepanja obrade pulpe nakon pranja s visokofrekventnim raspršivačem, strojem za uvijanje, drobilicom s diskovima, rafinerom s diskovima ili odvajačem kako bi se olabavila vlaknasta struktura.
19. Upotreba jedne nebijeljene slamnate pulpe za proizvodnju proizvoda od papira prirodne boje prema bilo kojem od zahtjeva 1-3, naznačena time, da se koristi nebijeljena slamnata pulpa sa vlačnom čvrstoćom od 230-280 mN, vlačnom čvrstoćom pri ponovljenom zavoja od 40-90 puta i permanganata numeracije 16-28.
20. Primjena prema zahtjevu 19, naznačena time što duljina loma navedene nebijeljene slamnate pulpe iznosi 5,0-7,5 km, bjelina je 25-45% ISO, stupanj rafinacije pulpe je 32-38°SR, pretežno duljina loma odabrane navedene nebijeljene slamnate celuloze - 6,5-7,5 km, bjelina - 35-45% ISO, stupanj mljevenja celuloze - 32-36°SR, bjelina - 35-45% ISO, vlačna čvrstoća - 250-280 mN, lomna čvrstoća kod ponovljenih zavoja - 65-90 puta.
21. Upotreba prema zahtjevu 19, naznačena time što faza dobivanja navedene nebijeljene slamnate pulpe uključuje kuhanje, pranje i delignifikaciju kisikom, uklj. Poželjno je dobiti slamnatu celulozu visoke tvrdoće s permanganatnim brojem 16-23 i stupnjem mljevenja 10-24°SR nakon kuhanja sirovina iz usjeva žitarica.
22. Primjena prema zahtjevu 19, naznačena time, da navedene faze dobivanja nebijeljene pulpe slame uključuju kuhanje, pranje i delignifikaciju kisikom, navedena delignifikacija kisikom se sastoji od pumpanja visoko tvrde celuloze s permanganatnim brojem 16-28 nakon kuhanja uz dodatak lužine i kisika u delegnifikaciju u stupcu reaktora s kisikom, kao rezultat reakcije delignifikacije nastaje celuloza s permanganatnom tvrdoćom od 10-14, poželjno je da se delignifikacija s kisikom provodi u jednom stupnju, reakcija se provodi u reaktoru za delignifikaciju s kisikom -koloni, temperatura i tlak navedene visokotvrde celuloze na ulazu i izlazu iz ove reaktorske kolone su 95-100°C, 0,9-1,2 MPa i 100-105°C, 0,2-0,6 MPa, u procesu delignifikacije kisikom, potrošnja NaOH lužine je 2-4% potrošnje apsolutno suhe celuloze, potrošnja kisika je 20 -40 kg/t apsolutno suhe celuloze, vrijeme reakcije - 60-90 min.
23. Primjena u skladu s patentnim zahtjevom 21 ili 22, u kojoj metoda proizvodnje kaše uključuje jednu od metoda amonijevog sulfita, metode antrahionske sode, sulfatne metode ili metode natrijevog sulfita, dok kod kuhanja metodom amonijevog sulfita, potrošnja amonijevog sulfita iznosi 9-13% potrošnje apsolutno suhih sirovina, pri kuhanju antrakinon-natrijevom metodom, potrošnja NaOH lužine iznosi 9-15% potrošnje apsolutno suhih sirovina, pri kuhanju sulfatnom metodom, potrošnja NaOH lužine je 8-11% potrošnje apsolutno suhih sirovina, pri kuhanju sa sulfitom - natrijevom metodom, potrošnja kaustične kiseline je 11-15% težine apsolutno suhih sirovina, potrošnja natrija sulfit je 2-6% težine apsolutno suhe sirovine.
24. Primjena prema zahtjevu 21 ili 22, naznačena time, da se pranje sastoji od:
(1) pumpanje pulpe visoke tvrdoće s koncentracijom od 8-15% u prešu, cijeđenje crne lužine iz pulpe i dobivanje proizvoda s koncentracijom od 18-25%, gore opisana odabrana preša je prijelazna preša, jednopužni , dvostruki vijak ili dvostruki valjak,
(2) za pranje celuloze nakon cijeđenja, koje se provodi u vakuumskom ispiraču, tlačnom ispiraču ili vodoravnom trakastom ispiraču, crna tekućina koncentracije 3-6,2 ° Be" i pH vrijednosti 8-8,3 na temperaturi od 70-80°C, ili voda na temperaturi od 70-80°C, ili crna tekućina i voda.
Slični patenti:
Izum se odnosi na proizvod od suhog papirnog papira, posebno na proizvod od suhog papirnog papira prikladan za proizvodnju pjene od sapuna, na metodu za izradu takvog papira, na metodu za čišćenje tvrde površine korištenjem navedenog papira i na upotrebu navedenog papira za čišćenje tvrdih površina.
Izum se odnosi na industriju celuloze i papira, na sastav celuloze za proizvodnju premazanih vrsta papira, zahtijevajući Visoka kvaliteta bazni papir se posebno može koristiti za proizvodnju lakog premazanog papira.